How to build an oak frame home step-by-step, according to the experts
We went to the experts to outline the steps needed to help guide you through a smooth and successful oak frame build journey
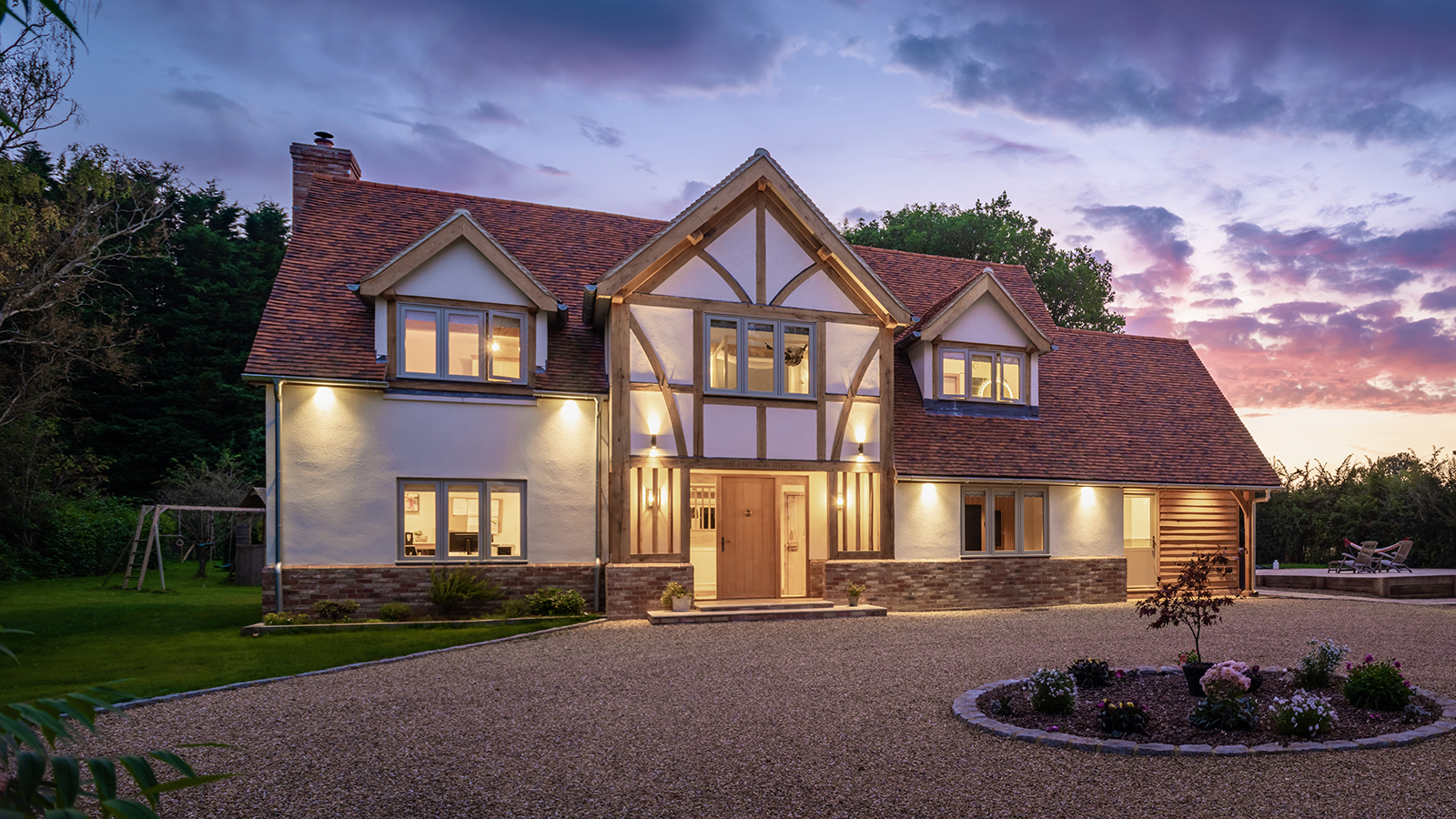
- 1. Find a plot
- 2. Designing your home
- 3. Set out your budget
- 4. Apply for planning approval
- 5. Decide on your oak frame style
- 6. Consider other build materials
- 7. Decide on your build route
- 8. Foundations laid
- 9. Construction of the oak frame
- 10. Frame is wrapped
- 11. Exterior and interior fit-out
- FAQs
Knowing the essential steps for how to build an oak frame home could be the deciding factor as to whether this characterful construction method is for you.
While homebuilding has an ever-increasing focus on biophilic and sustainable design, oak frame homes may pique the interest of self-builders looking to create green and healthy living spaces.
"As the UK's oldest vernacular construction methods, not only does green oak framing have a ‘tried and tested’ heritage, but it is also super sustainable, beautiful and strong, and people feel a genuine affinity with natural materials and craftsmanship," says Merry Albright, creative director of Border Oak.
How to build an oak frame home step by step
Oak frame properties are beautiful and full of character, and as a construction method, the frames are quick to go up. Providing you get a quote for your oak frame project through a reputable company, a reliable way to build a house.
1. Find a plot for building your oak frame home
"There are lots of different ways of finding a plot – some luckily have a large garden that can be divided and built on, others might buy a run-down house to replace. Some plots appear on the open market with estate agents, but many are sold via word of mouth," begins Merry Albright.
When making sure your plot is big enough, remember you’ll need space around the site to store materials, and tools for erecting the structure (this could mean hiring land from a neighbour).
Standard oak frame guides also highlight the need for an access road that is at least three metres wide for an articulated truck and crane to deliver and erect the house frame and encapsulation.
There are oak frame companies that buy land to create specific plots for oak frame homes, providing the services, planning and full build packages, plus landscaping. The plots typically come in clusters of less than 10 homes.
"We sell these plots to our clients who commission us to undertake the construction work to their specifications and budget," explains Merry. "We also work with landowners to achieve planning approval and create plots on their land – before making these available to our clients and working in partnership with the landowner to ensure the plots echo what our clients need."
It's important to consider planning permission for any plots, outlined in more detail later on in this article.
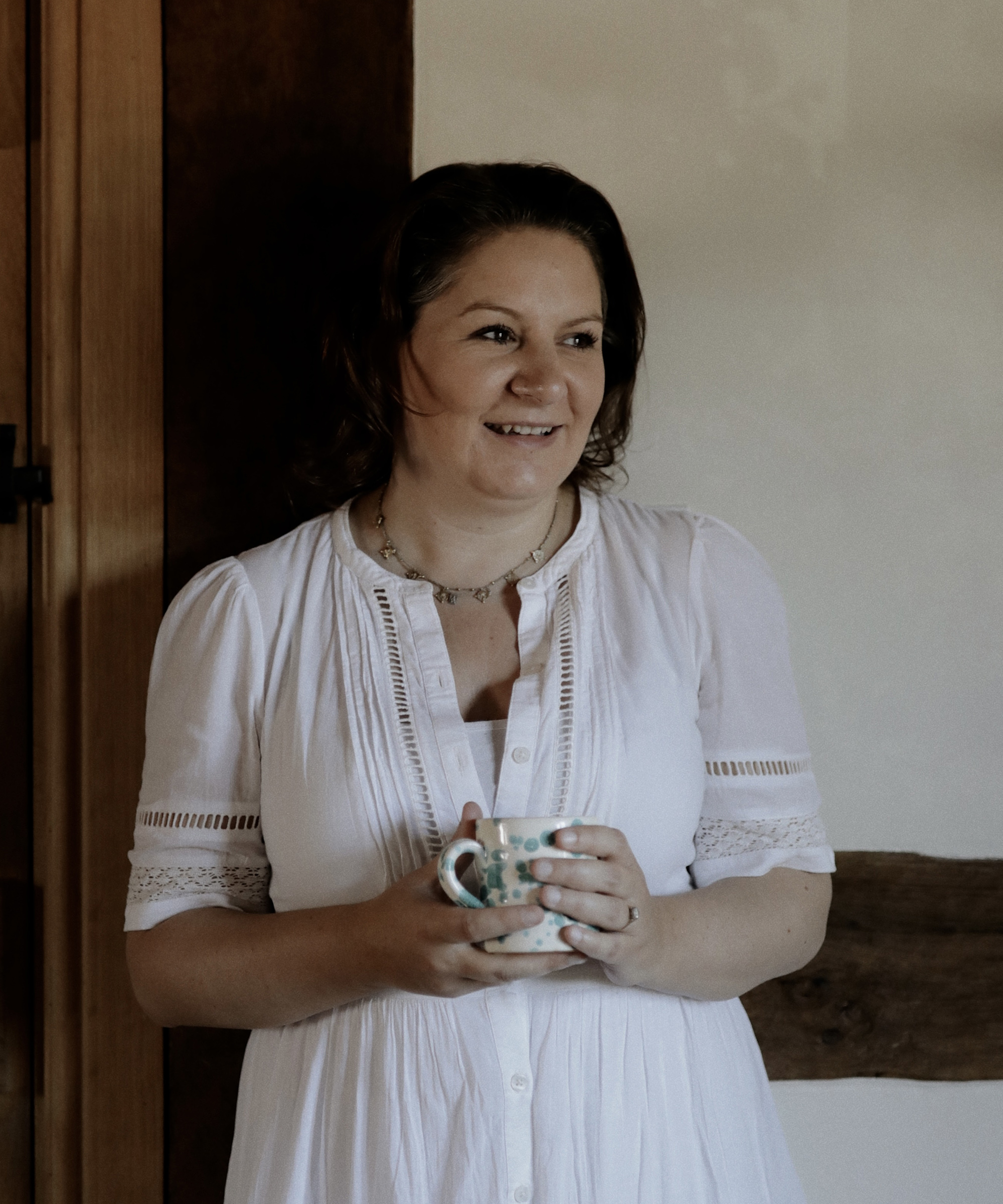
Merry is the creative director at Border Oak. She is involved with the architectural team creating new house designs, as well as on-site with the builders, to making presentations to Parish Councils and negotiating with planning officers.
Other options for finding a suitable plot are:
- National land databases such as Plotfinder.net
- Local press
- Auctions
- Estate agents
- Builders
2. Designing your perfect oak frame home
When it comes to designing your oak frame home, it is important to appoint an architect or designer who is experienced in this build method," explains Paul Edmunds, founder of Welsh Oak Frame. "This will avoid complications further down the line.
"Many oak frame companies offer an in-house design service which is often cheaper than architect fees.
"One of the first things you need to do when designing a house is to develop a brief. Begin by considering the things that you need in your home, and things that you would like in your home. It’s also useful to list the things you don’t like."
Paul outlines a list of questions to consider below:
- Do you prefer open or closed plan?
- How many bedrooms do you need?
- Do you want them to have en-suites?
- What are your desired sustainable standards?
- What storage area do you need?
- Would you like a separate utility room?
- What materials are you going to use?
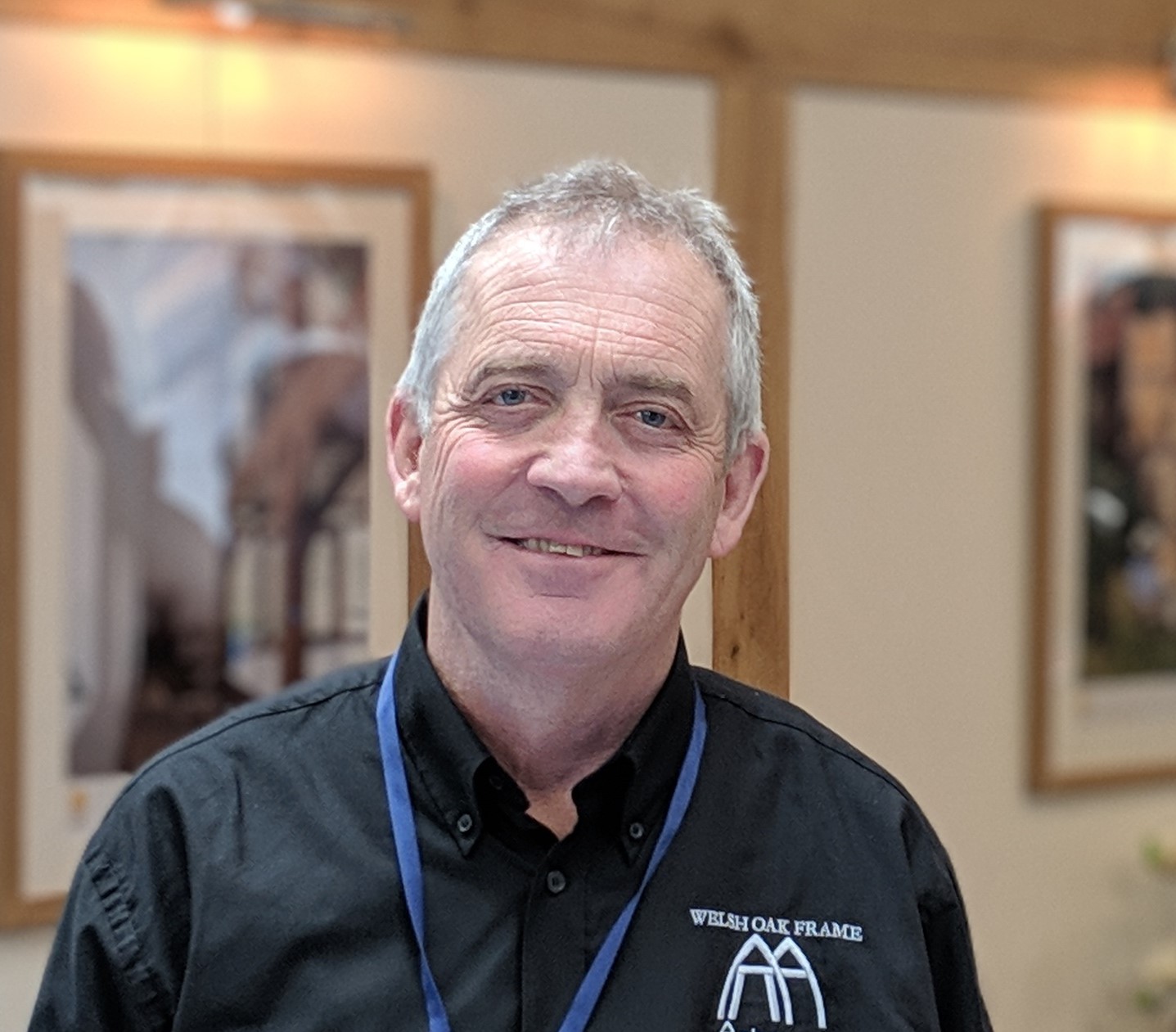
Paul is the founder of Welsh Oak Frame who have been designing and constructing oak frame homes and extensions in the UK for over three decades.
3. Set out your budget for the build
An important thing to know before building an oak frame home is to be clear about your budget from the start. Paul Edmunds suggests that budgets should be set out in tandem with the design of your oak frame house as it can affect the complexity of the overall design; "it will also impact the frame style and volume of oak that can be incorporated into your home," says Paul.
"Working with a specialist oak frame designer is essential if you’re keeping to a tight budget. They’ll be best placed to advise on how to make the most of the system while keeping costs down."
"Once the architect/designer understands your requirements, your site and how much it costs to build your oak frame home, they will produce a set of draft plans. This is an exciting stage where you will start to see your dream home coming together. After you agree on the final design, your drawing package will be ready to be submitted to the local planning authority for advice or approval," says Paul.
4. Apply for planning approval for your build
"The planning process for an oak frame home is no different to any other home, however, the adaptable styles of the exterior finish and ease of integrating an oak frame home into local vernacular, even with contemporary oak frame homes, can be favourable to planners," says Helen Needham, Head of Architecture at Oakwrights.
"Buying land with planning permission already in place gives you the assurance you’ll be able to build a house on the site," explains Paul Edmunds Founder of Welsh Oak Frame.
"Land sold with outline planning permission (OPP) is an agreement in principle that a house of a certain size can be built but the finer details – called ‘reserved matters’ – haven’t been agreed, such as its appearance, scale, access. You’ll have three years to finalise the design."
Then there is land with detailed planning permission (DPP). "This means the house design has already been approved as per the detailed set of drawings showing the property’s elevations and floorplans, external materials, and site plan. If you buy land with DPP you don’t have to stick to the approved design. You can submit a new application for a different design but you’ll be starting from scratch," adds Paul.
Buying land without planning permission can be risky, leading to delays and even disappointment if you are unable to secure the permission you need.
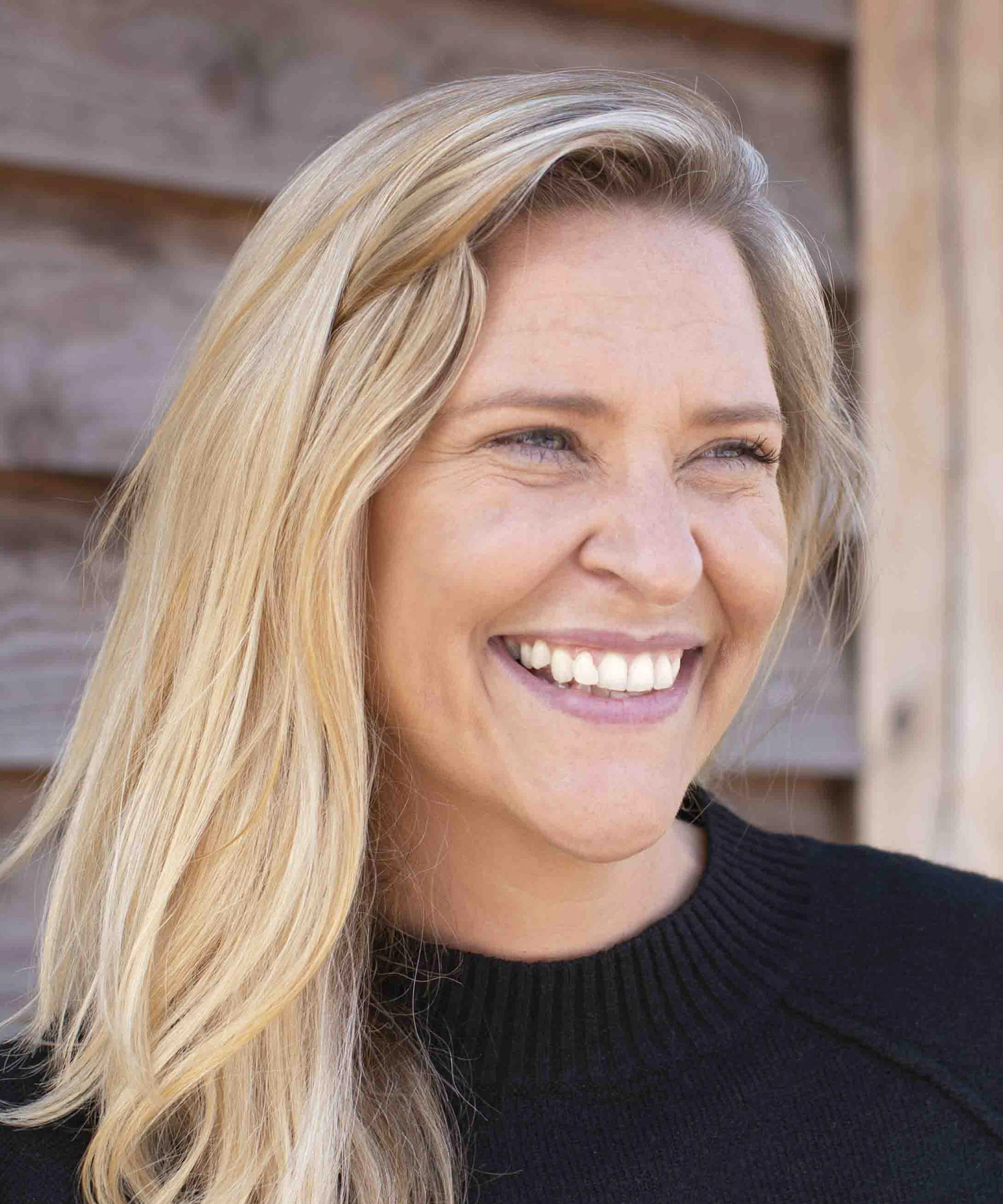
Helen heads up Oakwrights' architectural service, facilitating some incredible designs from Design and Planning, through to Building Regulations and Technical Detailing.
5. Decide on your your style of oak frame
"When we talk about oak frame styles, we are referring to the overall aesthetic you would like to achieve and the amount of oak you would like to see exposed in your new home or oak frame extension. The style of home you are looking to achieve will largely dictate how much oak is required," says Paul Edmunds.
"Traditional styles generally require the most amount of oak, usually exposed both internally and externally. Barn styles tend to have a more simple footprint and are usually more open plan with less oak exposed. Post and beam layouts work on a simple grid system and require even less oak."
"Adopting a hybrid approach, reserving oak for those high-impact areas and using a hidden softwood frame in the less important rooms, is a great way to add character to your home and at the same time, save money," says Paul.
Many self-builders choosing oak frames go down the encapsulation route, where all or part of the frame is wrapped in an insulated shell, which can then be clad in the finish of your choice — render, brick, timber boarding, tile hanging and so on.
6. Consider the materials you will be using to wrap your home
"Oak frames can have different panel encapsulation systems that effectively wrap around the structural oak frame depending on the design," explains Merry Albright.
"We work in oak frame, softwood timber frame, SIPs (structural insulated panels) and masonry – very often in combination with one another depending on the design."
Then there is the option to achieve the Passivhaus standard with your chosen construction system as Helen Needham explains:
"By integrating pre-insulated panels, MVHR (Mechanical Ventilation with Heat Recovery), and the timeless aesthetics of oak, we create healthy, energy-efficient living spaces. MVHR ensures clean, filtered air at a comfortable temperature, enhancing the living experience."
7. Decide on your build route
"Deciding on how you wish to project manage your self-build is a personal choice and depends on what you wish to get out of the experience as well your budget, your time available and the level of responsibility you wish to take on," explains Charlie Mills, Managing Director at Oakwrights.
Here Charlie outlines the different self build routes you can take when thinking about how to build an oak-frame home:
- Traditional self-build: The most hands-on approach which will be the cheapest but most laborious. You will act as the principal contractor and do most of the build yourself.
- Self-project managing your build: With this route, you are handling everything except the building work and acting as the official principal contractor.
- Appointing a builder as Principal Contractor: this hands over the building site management to a professional. Your builder will manage Health & Safety on site, work with Building Control to gain approval and engage all your specialist trades for you, you will still have to be on-site regularly
- Turnkey service: The most hands-off, stress-free but inevitably priciest option. Other than being involved in design decisions your oak frame home will essentially be built for you by the oak frame company with no need for you to be there.
8. Work starts with the foundations being laid
Once you have decided on a design, the structural load of the frame will be calculated. This is usually best handled by your oak frame supplier or an engineer with specific oak frame experience. Your foundation system is dependent on ground conditions too.
Some frame companies offer the foundations as part of the service as it can be beneficial to have one set of people responsible for both elements which are interlinked.
"Ground workers will prepare the foundations for your home with pads for the oak posts and perimeter blockwork for the wall panels. Your oak frame and wall and roof system will be being prefabricated in our workshops at the same time," explains MD of Oakwrights, Charlie Mills.
Your build team will prepare the base for the oak frame to sit on. The build team you choose is up to you, but often your oak frame supplier will be able to recommend trades they have previously worked with.
"Generally speaking, foundations take a couple of weeks," adds Juliette Lessware of Carpenter Oak.
9. Construction of the oak frame on site
It is at this point after your foundations have been laid, your chosen oak frame team will take over from the builders periodically. Charlie Mills highlights that if you choose to self-manage your project, this will be the only stage in which your oak framers will be involved.
The oak frame is delivered to the site, ready to be erected on your prepared base. According to Juliette Lessware, the oak frame can be raised in a matter of days (for extensions or oak frame conservatories) or a week or two for a house.
"Treating or cleaning your frame e.g. sandblasting, needs to be done before further work takes place, such as windows and glazing being installed," says Juliette.
"Don't forget that your oak framer should also provide Standard Details and an engineering certificate for Building Control," she adds.
10. Oak frame is wrapped with the encapsulation system
This is the phase that Juliette Lessware refers to as 'wrapping' during your timber frame construction. "Whether with SIPs panels or another system, this will get your build to the wind and weatherproof stage," she explains.
If you choose a pre-manufactured system like SIPs, Juliette says that wrapping can take as little as a couple of weeks. The system will 'enclose' the oak frame and provide the walls and roof. Whether you use SIPs or another type of timber-based system this incorporates insulation.
Many oak frame specialists will have their own particular encapsulation systems that they tend to use around the oak frame. They can construct this as well as put up your frame if you choose this option.
The internal stud walls are put together and joists are secured as the frame takes shape.
11. Exterior cladding materials are fixed and interior is fit-out
Once the frame is up, the exterior cladding materials can be fixed to the infill panels or encapsulation system. The roof covering is also fixed into place – the glazing can be fitted into the window openings too.
Whilst the exterior cladding is being fitted the interior fit-out can commence. This will involve your first and second fix electricals and plumbing so it is essential that the house is weathertight.
If you're looking to achieve air-tightness, Charlie Mills points out that the first fix is the stage which you would do this using AeroBarrier or similar.
Plasterboard or drylining board can also be fixed into place, underfloor heating installed, flooring finished laid and so on.
The length of time the fit-out takes to completion depends on a few factors. "The fit-out could take anything from a few months to a year (or longer!) depending on how quick your main contractor is, how large your home is and how you're finishing your home," says Juliette Lessware.
FAQs
How long do oak framed buildings last?
"The use of oak in buildings in the UK can date as far back as 998 AD," says Paul Edmunds Founder of Welsh Oak Frame.
"Oak framing has been used to craft the nation's homes for centuries. This is because it is one of the most durable building materials that you can build with," he says.
In terms of modern oak-framed homes Merry Albright of Border Oak explains: "Newly built oak-frame homes are almost over-engineered, so if they are looked after they should also last hundreds of years. They are also very adaptable so can be varied should needs change."
The moment your house is truly ready is when the scaffolding finally comes down and any last bits of decoration and landscaping can take place.
To help achieve the look you want surrounding your new oak frame home, take a look at our list of garden landscaping ideas.
Bring your dream home to life with expert advice, how to guides and design inspiration. Sign up for our newsletter and get two free tickets to a Homebuilding & Renovating Show near you.
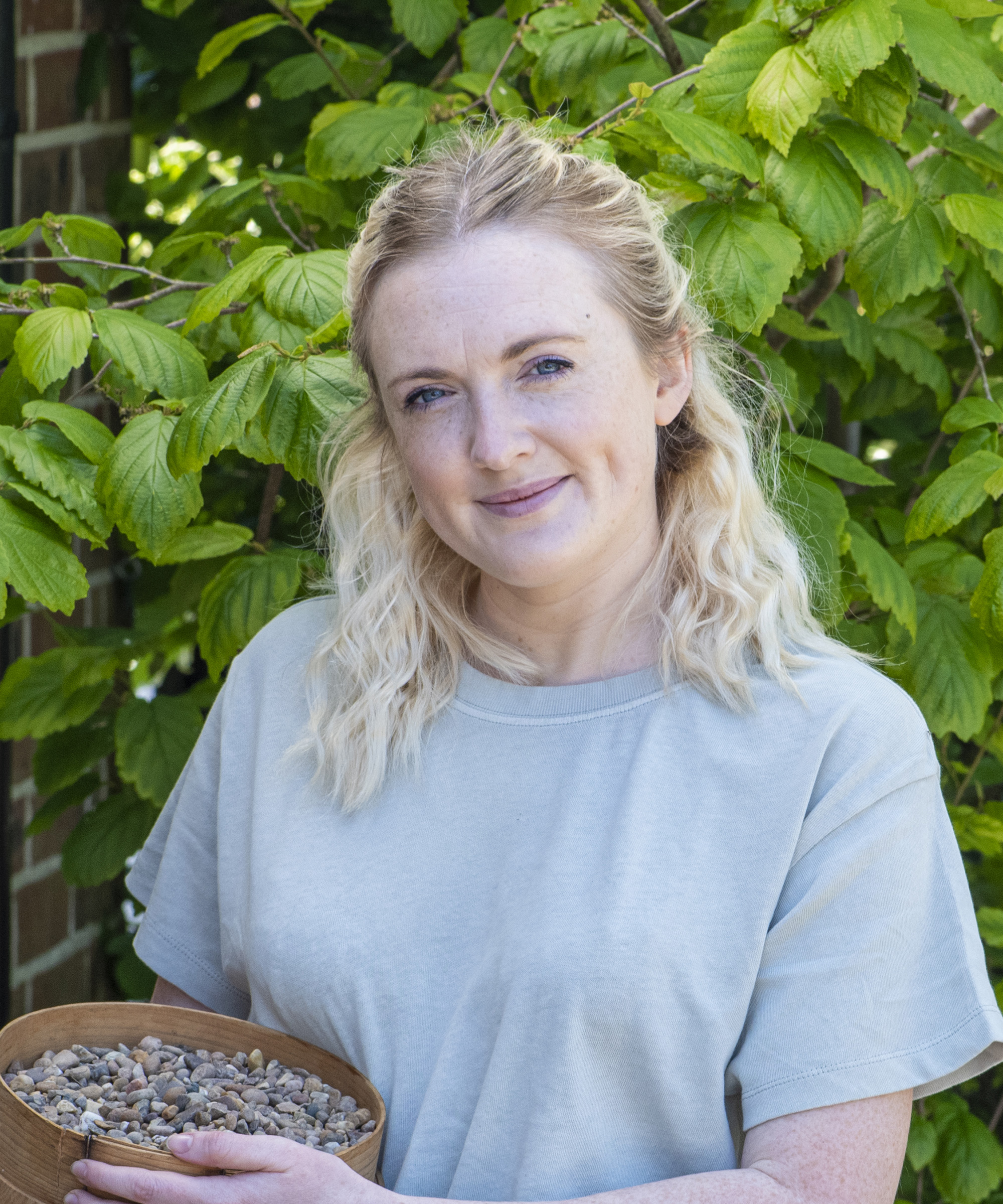
Teresa was part of a team that launched Easy Gardens in 2018 and worked as the Editor on this magazine. She has extensive experience writing and editing content on gardens and landscaping on brands such as Homes & Gardens, Country Homes & Interiors and Living Etc magazine. She has developed close working relationships with top landscape architects and leading industry experts, and has been exposed to an array of rich content and expertise.
In 2020 Teresa bought her first home. She and her partner worked alongside architects and builders to transform the downstairs area of her two bedroom Victorian house in north London into a usable space for her family. Along the way she learned the stresses, woes and joys of home renovation, and is now looking to her next project, landscaping the back garden.