Types of brick: Colours, costs and the best options for your build
What are the different types of brick to choose from? The answer is more complicated than you think

Selecting the right type of brick is one of the most important decisions when building a house or extension.
Not only do bricks form the foundation of your structure, but they also define its character, influence its energy efficiency, and impact the environment.
With a wide variety of brick types available in the UK, there’s an option to suit every architectural style, budget, and sustainability goal.
In this guide, we’ll take you through the different types of brick, including the latest eco-friendly innovations, and help you choose the perfect fit for your project.
What are the main types of brick in the UK?
Each type of brick offers unique benefits in terms of aesthetics, durability, and sustainability.
Here’s a breakdown of the most common options you’ll encounter - from traditional clay bricks to cutting-edge carbon-neutral varieties.
Clay bricks
Clay bricks are the most widely used and versatile brick type in the UK. Made from natural materials and fired in kilns, they offer durability, colour consistency and wide-ranging styles to suit everything from Georgian terraces to contemporary builds.
Their natural look and performance characteristics make them a solid choice for most residential projects.
Extruded (wire-cut) bricks
These machine-made bricks are manufactured by pushing clay through a die and cutting it to size with wire.
The result is a uniform, sharp-edged brick that’s often perforated to reduce weight and drying time. Wire-cut bricks are particularly well-suited to modern builds thanks to their precision and affordability.
“Extruded bricks often have perforations, which make them lighter and easier to handle while reducing drying energy,” says Scott Hosie, Senior Product Manager at Forterra.
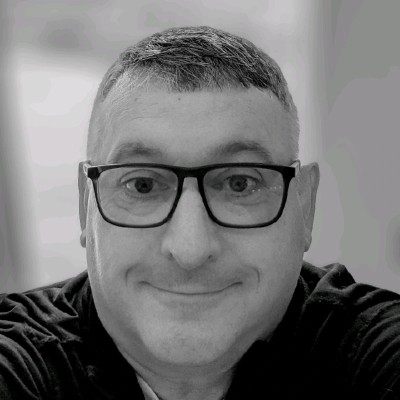
Scott Hosie plays a leading role at Forterra, one of the UK’s largest brick manufacturers. With deep technical knowledge of clay products and masonry construction, he advises on brick specification, performance, and compliance.
Soft mud and waterstruck bricks
For a more rustic look, soft mud bricks are created by throwing clay into sand-coated moulds.
This process produces gentle irregularities and surface textures that lend character to period-style homes. Waterstruck bricks, formed with water-lubricated moulds, offer a smoother texture but retain a hand-crafted aesthetic.
Handmade bricks
For heritage projects or homes seeking an artisan feel, handmade bricks are unmatched. Each brick is shaped by hand, giving rise to unique imperfections and colour variations that create rich visual depth.
“Handmade bricks allow for a more flexible, characterful build with an authentic aesthetic,” explains Jason Hughes, Managing Director of Imperial Bricks.
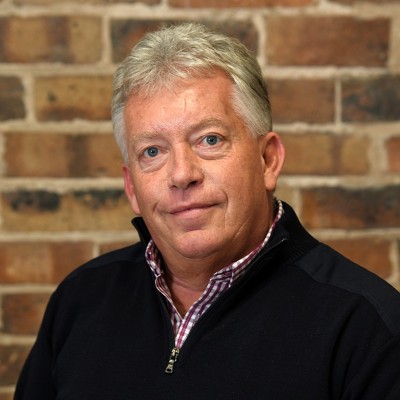
Jason helps supply over 150 million bricks annually specialising in regional styles, conservation projects through Imperial Bricks, who are the UK’s only producer of both tight-textured sandstruck and waterstruck bricks.
Reclaimed bricks
Reclaimed bricks are salvaged from old buildings and reused, offering a low-carbon footprint and a ready-made patina.
They’re ideal for conservation areas or for matching materials for extension - though sourcing them in large quantities can be challenging.
Carbon-neutral bricks
One of the new types of brick is the carbon-neutral brick developed by Seratech, a UK-based climate-tech start-up working with Imperial College London.
This brick cures at ambient temperatures, eliminating the need for high-energy kilns, and can even store CO₂ from industrial processes - making it truly carbon-neutral.
This carbon-neutral brick can store carbon within the home itself, helping to reduce overall emissions.
Recycled bricks (K-BRIQ)
Another breakthrough is the K-BRIQ, which is made from 90% recycled construction and demolition waste.
It avoids firing altogether, cutting its embodied carbon by up to 95%. Already certified for use in the UK, this brick is helping to shift the industry toward circular building practices.
Bricklaying must-haves
Choosing the right brick colour and finish
While structural and environmental factors matter, the colour and finish of your bricks also play a major role – especially if your build needs to comply with local planning constraints.
Brick colours are often regionally specific:
- Red bricks dominate in the North and Midlands
- Buff and yellow bricks are common in London, Essex, and the South East
- Cream or orange tones appear in the Cotswolds and parts of Lincolnshire
- Blue engineering bricks are a hallmark of the Midlands
“The colours of bricks are determined by their position in the kiln and firing temperatures,” says Jim Matthews of H G Matthews Brickworks.
To ensure visual consistency, always mix bricks from different packs before laying. This avoids banding and creates a more natural finish.
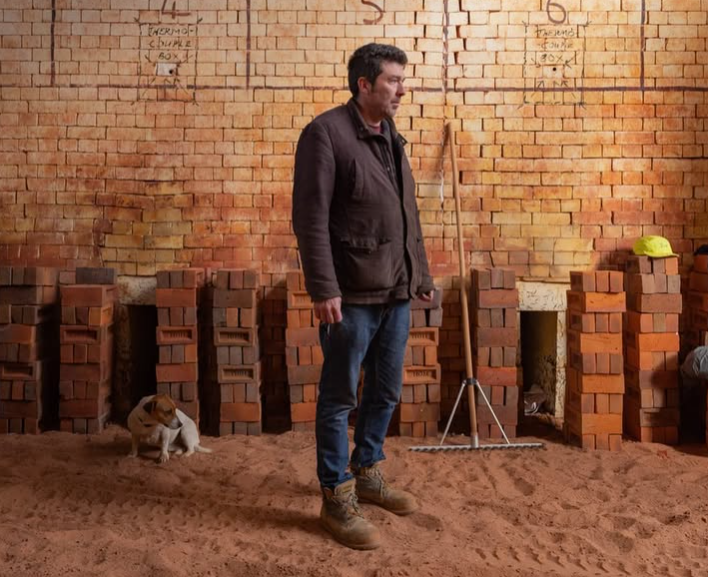
Jim Matthews is the manager of H G Matthews Brickworks who have been creating bricks since 1923.
Understanding brick sizes and bonds
Once you’ve chosen a brick type and colour, consider the dimensions and the way the bricks will be laid – known as the bond.
These factors influence both the final look and the structural stability of your build.
- Metric bricks (215mm x 102.5mm x 65mm) are standard today
- Imperial bricks (commonly 9in x 4.5in x 3in) are needed for period property repairs
Popular brick bonding patterns:
- Stretcher bond: A modern standard using only the long face (stretcher) of the brick
- Flemish bond: Alternates headers and stretchers for a traditional appearance
- English bond: Offers superior strength using alternating courses of headers and stretchers
- Stack bond: Visually striking, but structurally weaker unless reinforced
What do different types of brick cost?
Budget is a critical consideration when selecting bricks. Costs vary depending on manufacturing method, sustainability credentials and aesthetic value.
Brick Type | Typical Cost (per 1,000) |
---|---|
Wire-cut bricks | £250–£400 |
Handmade bricks | £600+ |
Reclaimed bricks | Variable; often higher |
Keep in mind that handmade and reclaimed bricks also tend to have higher waste allowances due to breakages and variations. Factor in about 5–10% extra bricks to be safe.
Cheap bricks are an option if cost is important, but you may want to consider blocks instead if you are less concerned about aethetics.
You can estimate how many bricks you’ll need using a calculator. A standard wall in stretcher bond requires about 60 bricks per m².
Best way to buy bricks
You can purchase bricks from national merchants like Travis Perkins, Forterra or other builders merchants.
If you’re looking for reclaimed or handmade bricks, specialist yards or manufacturers like Imperial Bricks are your best bet.
Before ordering:
- Request a brick matching service if you're blending new bricks with existing ones
- Check whether pre-weathered or tinted bricks are needed to meet planning permission requirements
- Confirm availability, especially for bespoke or reclaimed options, as lead times can vary
Choosing the right mortar
Choosing the right mortar is essential to complement your bricks – both visually and functionally.
For softer bricks like handmade or reclaimed varieties, lime mortar is often the best choice due to its flexibility and breathability.
“It allows for natural movement and reduces the risk of frost damage,” adds Jason Hughes of Imperial Bricks.
Mortar colour can subtly shift the tone of your brickwork, so be sure to test samples before committing to a mix.
Once you have chosen the right type of brick there are a few other key considerations to help you finish your project to the highest standard.
If you're looking to create a feature wall or achieve a traditional look without the weight or depth of full bricks, brick slips offer a clever, space-saving solution.
For those working on extensions or renovations, brick tinting can help ensure new brickwork blends seamlessly with existing walls. And if you're restoring an older property, you might need advice on removing paint from brick to bring back the natural texture and colour of the original materials.
Finally, once you've made all your choices, make sure your bricks are laid properly and professionally using our guide to finding a bricklayer to ensure your project is in expert hands.
Bring your dream home to life with expert advice, how to guides and design inspiration. Sign up for our newsletter and get two free tickets to a Homebuilding & Renovating Show near you.
Michelle was Homebuilding & Renovating magazine's Deputy Editor. With an editorial career spanning more than 18 years, Michelle spent time working on educational magazines and websites until her career took an exciting turn into the world of homes and interiors. Working on sister titles Real Homes and Period Living, she then joined the Homebuilding team in November 2018.
She’s just completed her second kitchen renovation project and bathroom renovation, armed with an ever-growing knowledge of homebuilding advice and design inspo (and a Pinterest board or two, of course).