Building Regulations Part F: How the New Ventilation Changes Could Affect You
Changes to Building Regulations Part F take effect from 15 June which could impact extenders and renovators
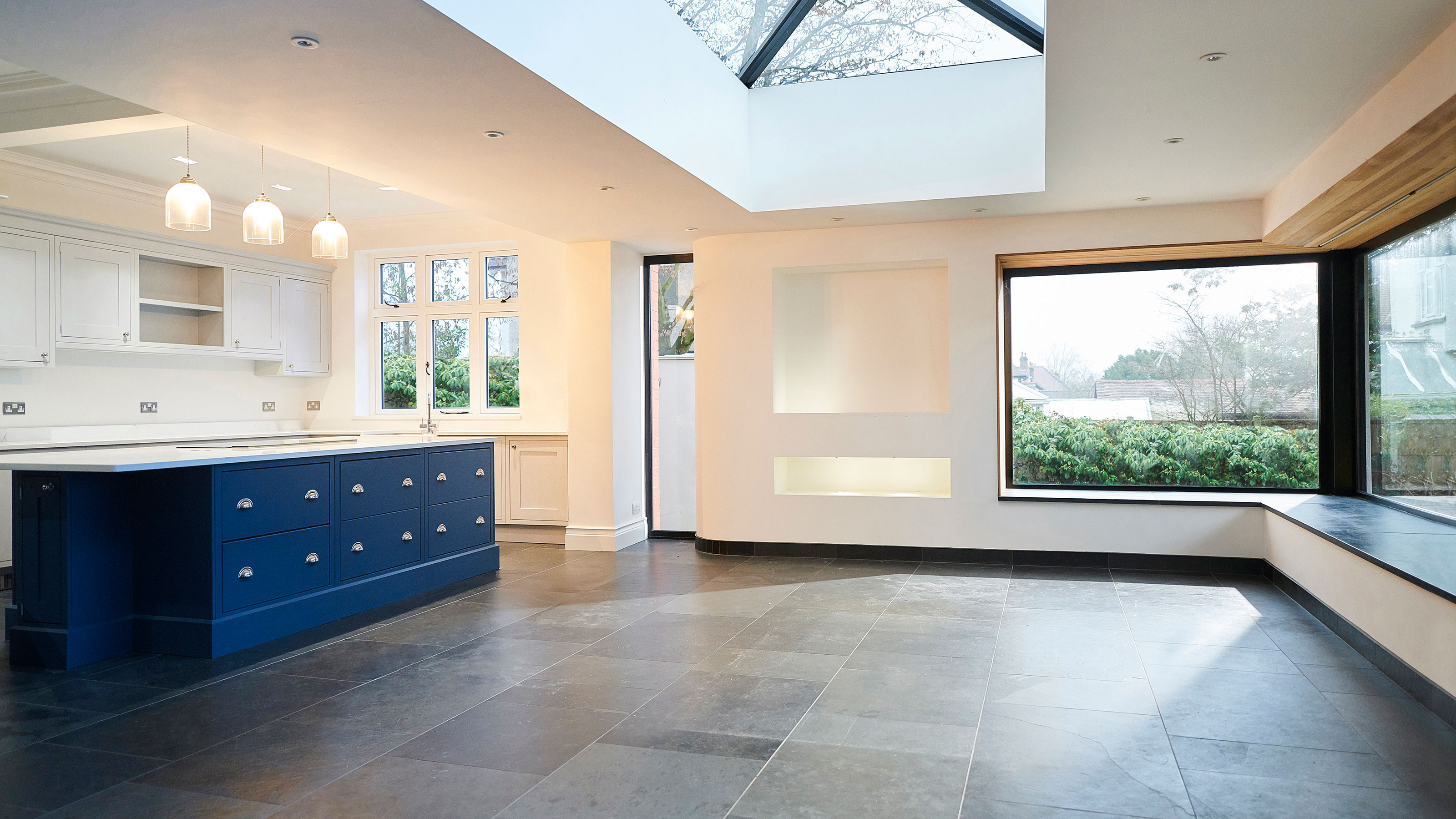
Building Regulations Part F covers a topic that has been relatively overlooked in our home's energy efficiency make-up: ventilation. Up until very recently, we all concentrated on insulation to increase the efficiency of our homes but airtightness in new and existing properties is now something that is imperative if an energy-efficient result is required.
Ventilation is crucial for a warm, airtight home, but it is often the forgotten part of the energy efficiency equation. Insulation is great, and more is better, but even a highly insulated wind tunnel will not hold heat. If your house isn’t airtight then the insulation applied cannot work properly, as the heat is simply lost in the air.
Ventilation is enshrined as part of Building Regulations in Approved Document F, and from 15 June 2022 the regulations are changing, which could affect anyone undertaking a home improvement project, extension, renovation or self build.
Here's what you need to know about Part F, the new regulations, and how the changes will apply to your project.
What is Building Regulations Part F?
Building Regulation Part F covers ventilation in properties in England and most of the details can be found on the government website. The documents on this page are designed to ensure that ventilation not only delivers the required airflow, but also does so efficiently and quietly.
There are effectively four different ventilation ‘systems’ that are described in Part F (which I’ll expand upon below) and if you’re undertaking a self build then you will need to comply with one of these system’s regulations to be passed by building control.
Each of these systems has an implication on cost, disruption and overall energy efficiency of the property, so this is certainly something that needs to be detailed at the brief stage or you may end up with the system that you didn’t choose or one that does not work.
Bring your dream home to life with expert advice, how to guides and design inspiration. Sign up for our newsletter and get two free tickets to a Homebuilding & Renovating Show near you.
What Are The New Regulations?
In December 2021 the government announced that several new Building Regulations would affect homeowners and homebuilders from 15 June 2022. One of these is an interim uplift to Part F, and it could have a major impact on those renovating a house, adding an extension or taking on home improvements.
The uplift includes a new requirement that when any improvements, extensions or renovations are done to a building, the ventilation is no worse than before the works began. The works must also comply with all regulations concerning controlled services such as cookers, boilers, fires or electrics.
Part F also now recommends that all installations of mechanical ventilation products (more on this below) come with guidance on why ventilation is important. A commissioning sheet and checklist including all the design flow rates, commissioned flow rates, for both boost and trickle rates, will also be provided.
Moreover, there will be a recommendation that all replacement windows are fitted with trickle vents unless there is an alternative form of ventilation, such as air bricks or whole house Mechanical Ventilation with Heat Recovery (MVHR), or indeed that the works do not result in the ventilation being worse than before the works were done.
The government has been criticised for not going far enough with the new changes, however. Chris Herring, director at Green Building Store, says: "Airtightness is as important as insulation, but it seems clear that in the current uplift there is no intention to address this.
"Fundamentally the government needs to address this issue and significantly tighten airtightness levels and move to mechanical ventilation. This would need some time to implement because the industry and supply chain for mechanical ventilation is not mature, but we will never achieve high-quality building fabric without it."
When do The New Regulations Come in?
Changes to Approved Document F: Volume 1 (Dwellings) come into effect on 15 June 2022, however a grace period will take effect until 2023 for projects that are currently still in the building process.
This means that if you have applied for a building notice or initial notice before 15 June 2022, your project will still be considered under the previous regulations, provided building work begins before 15 June 2023.
Why Have the Regulations Been Updated?
Good ventilation is critical for the health and wellbeing of the occupants of a building, but efficient ventilation is crucial if we want to persuade people to not turn the ventilation units off to ‘save energy’.
As you make your home more airtight the insulation will be working properly but you will also get increased condensation due to the lack of air movement. You have to move the vapour out of an airtight building and this has to be done in a controlled manner.
Some might ask why we need these changes and the truth is that many homes are indeed getting more airtight and that the rooms are also becoming smaller. This leads to less volume of air for each person and less changes of that air, which in turn means the quality of the air is significantly worse.
Add that to the fact that many of us are now spending a lot more time at home due to flexible working or permanently working from home and you have the perfect storm for stale air.
Moisture in the home does not just disappear and a continuous turnover of ventilation is the best way to mitigate the vapour in the air condensing somewhere in the fabric of the home and forming unhealthy products such as mould. The ventilation must be constant but it must also be managed so that you are not over ventilating and losing lots of your valuable heat.
Which Ventilation Systems are Covered?
The performance and methodologies for each of the ‘system’ approaches set out in Part F are the absolute minimum requirements needed to ensure that adequate air quality is provided for the occupants indoors. There are a number of sets of air flow rates that need to be complied with in each ‘system’ and I will describe these using litres per second (l/s). These details are for guidance and are not targets in themselves.
To build a healthy home, it is up to the homeowner to work with approved and certified manufacturers and installers to ensure that the best system is specified and that design and installation best practice is used to achieve Part F compliance. The occupant’s health and wellbeing could be at risk if these ventilation rates are compromised.
1. Background Ventilation and Intermittent Extract Fans
The most common approach to meeting the Building Regulations Part F is intermittent extract fans with background vents (i.e. trickle vents in the windows or air bricks in the walls).
Extract fans are located in all the wet rooms such as the bathroom, ensuite, kitchen and utility room. They must comply with providing the following ventilation airflow rates for minimum intermittent extract and whole building ventilation rate based on number of bedrooms and occupancy levels in the dwelling.
Minimum extract ventilation rates for intermittent extract systems are:
- Kitchen: 30 l/s adjacent to the hob or 60 l/s elsewhere
- Utility room: 30l/s
- Bathroom (including shower room or ensuite): 15l/s
- Sanitary accommodation: 6 l/s
Minimum extract ventilation rates for continuous extract systems are:
- Kitchen: 13l/s
- Utility room: 8l/s
- Bathroom (including shower room or ensuite): 8l/s
- Sanitary accommodation: 6l/s
And for whole dwelling ventilation, delivered either through continuous supply fans or background ventilators, the minimum whole dwelling ventilation rates are determined by the number of bedrooms. The rates can be found in Approved Document F: Volume 1
The whole house ventilation rate will also take into account the uninterruptable free area of any trickle vents and air bricks.
2. Mechanical Extract Ventilation
Purge ventilation needs to be present in each room and capable of extracting a minimum of four air changes per hour per room. A window or mechanical system would count as purge ventilation.
Mechanical extract ventilation (MEV) is a continuous ventilation system. This can be either a whole house centralised MEV system, or localised decentralised MEV (dMEV) fans.
A centralised MEV system is typically located in a loft space or hallway cupboard. Multiple ducts run from the kitchen, bathroom, ensuite and other wet rooms of a property to the MEV unit to simultaneously draw moisture-laden air from wet rooms to control humidity levels. The ducts are balanced on commissioning by the installation engineer to ensure the right air flow is achieved in each area. As the air is extracted, fresh air enters the home via trickle vents and air bricks in the fabric of the building.
dMEV fans are individual room fans which operate continuously to draw moisture from either the bathroom, kitchen, utility room or other wet room.
Continuous mechanical systems should include either manual or automatic controls (i.e. humidity sensors) to switch operate between trickle and boost modes depending on air quality.
There are versions of MEV systems that have automatically variable air vents, air quality sensors and controllable fan units. This is referred to as ‘on demand’ ventilation. The sensors control the fan unit according to air quality and the trickle vents also open and close according to humidity levels in that room, resulting in ventilation only operating when required. These systems make a lot of sense but there may also be pollutants, such as aerosols or drying paint, that are not triggered by the sensors. Always ensure that the system is fit for purpose.
There are also MEV systems built into exhaust air heat pumps that are built into the hot water cylinder. As the air is extracted from the home the heat is taken out by a very small heat pump and used to create the hot water in the cylinder. By using this method the heat in the home is not wasted to the atmosphere unless there is no hot water requirement.
3. Mechanical Extract Ventilation with Heat Recovery
MVHR provides fresh, filtered air, energy efficiency and a comfortable climate all-year round.
Stale, moist air is extracted out of wet rooms, including the kitchen, bathrooms, utility and ensuite rooms, and fresh air is brought back in to the living areas such as the bedrooms, lounge and dining room. The warm stale air and the incoming cold air pass through a heat exchanger and the heat is transferred from the stale air to the fresh air indirectly and a large percentage of the heat is thus recovered and not lost to atmosphere.
MVHR systems should always provide the minimum whole building ventilation rate as well as the minimum extract rates required in the wet rooms. The Extract and supply rates must be balanced.
The Domestic Ventilation Compliance Guide describes the whole house ventilation rate for homes as follows: 1 bed homes: 13 l/s, 2 bed homes: 17 l/s, 3 bed homes: 21 l/s, 4 bed homes: 25l/s, 5 bed homes: 29l/s but a minimum ventilation rate of 0.3l/s per m2 of floor area (including all floors) must also be maintained.
These figures assume that only one bedroom has double occupancy, and if there is a higher occupancy then you need to add 4l/s per occupant. There are also minimum extract rates of 13l/s in the kitchen, 8l/s in bathrooms, shower rooms and utility rooms, and 6l/s in a WC. If there are multiple ensuite rooms in a home, plus a utility as well as a couple of WCs then your balanced ventilation rate could increase and it is the largest of these rates that becomes the required ventilation rate.
These four systems allow for a lot of variation but if you want to avoid air vents in your windows and walls then system 4 is the only real option. It is also worth noting that if you are also building in accordance with other aspirational standards such as Passivhaus, then these air flows can sometimes clash with those, depending on the size of the home, number of bathrooms and the occupancy.
4. Passive Stack Ventilation
Passive stack ventilation systems guidance have been removed from the Approved Document F: Volume 1, but these systems can still be used to achieve regulatory compliance.
Passive stack is a non-mechanical approach to ventilation, which is based on two main types: convection or wind pressure.
The first uses the principle of convection, or air buoyancy, where the warm, rising, air currents allow the movement of air out of the dwelling at high level and fresh air enters through trickle vents and air bricks, or purpose made air inlet ducts. These ducts are located in various locations around the dwelling, or in the passive ventilation unit. The air can be warm due to occupancy, with ducts often installed in chimney stacks, or it can also be designed into a vaulted area with lots of glazing to allow the sun to warm the space, causing the convection.
The second relies on wind pressure. Prevailing wind creates a positive pressure on the windward side of the building and a negative pressure is created on the leeward side of the building as the wind moves away from it. The combination of the positive and negative air creates an air flow through the home as it pushes from one side and pulls from the other. In leaky homes this effect takes away the warmth in the home very rapidly, but if designed properly it can provide a very good ventilation solution.
Many of the better systems also have dampers on the ducts to limit the air flow in strong winds. This does add a bit of ‘active’ control but it also avoids the issue of over ventilation.
Unfortunately many passive stack airflow rates are very much weather- and occupant-dependent with a risk of over or under ventilating. If there is no wind or sun, and the home is not fully occupied, there could be a lower ventilation rate than what is required.
David is a renewables and ventilation installer, with over 35 years experience, and is a long-standing contributor to Homebuilding and Renovating magazine. He is a member of the Gas Safe Register, has a Masters degree in Sustainable Architecture, and is an authority in sustainable building and energy efficiency, with extensive knowledge in building fabrics, heat recovery ventilation, renewables, and also conventional heating systems. He is also a speaker at the Homebuilding & Renovating Show.
Passionate about healthy, efficient homes, he is director of Heat and Energy Ltd. He works with architects, builders, self builders and renovators, and designs and project manages the installation of ventilation and heating systems to achieve the most energy efficient and cost effective outcome for every home.