Considering underfloor heating? How to choose the right system for your project
An increasingly popular option, underfloor heating systems are suitable for lots of different projects, whether you're building from scratch, renovating or extending. We explore the options and how to pick the best solution for your home
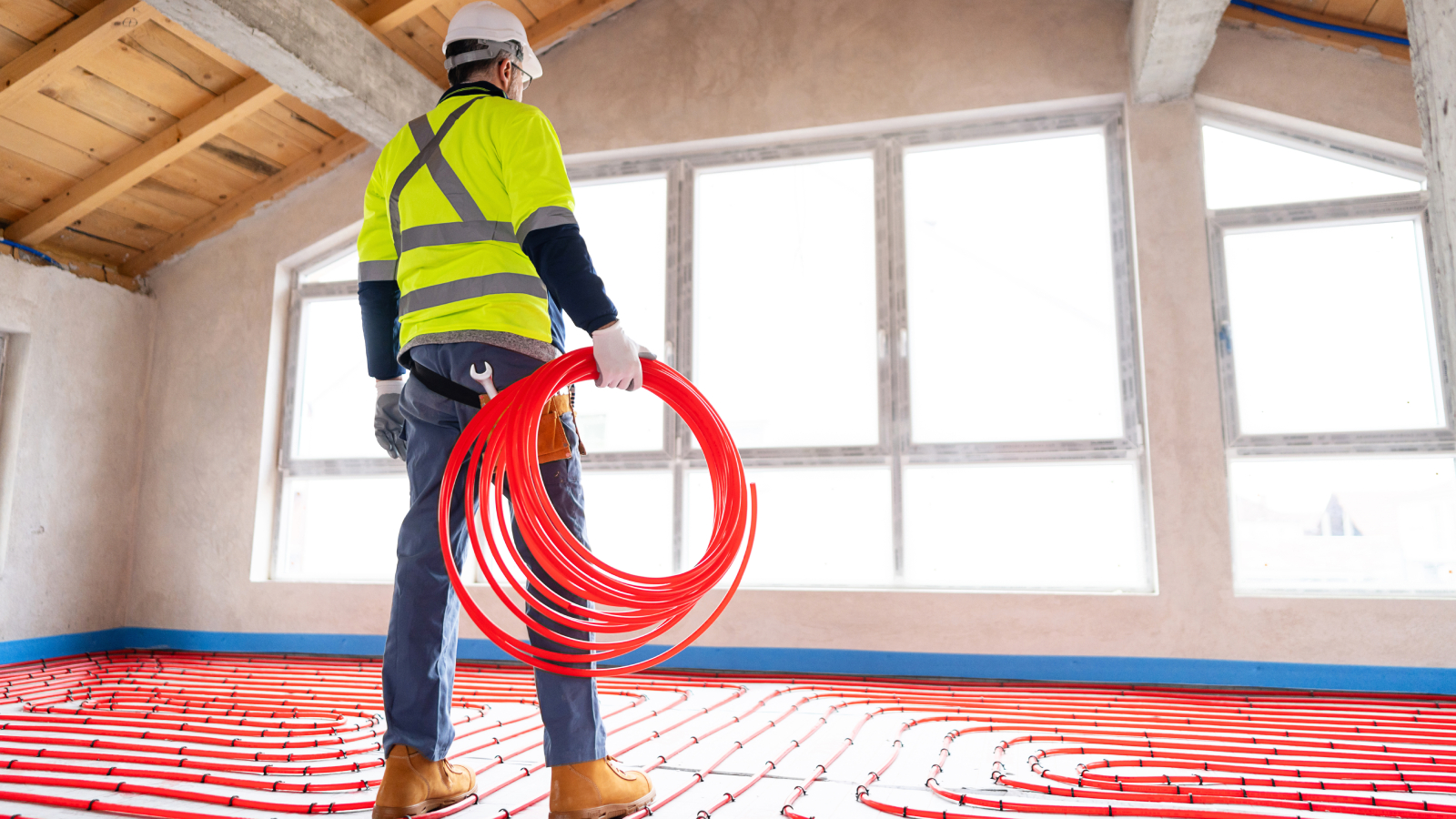
While underfloor heating was once considered mainly an option for new builds or extensions, developments in product ranges and technology means it's now a viable option for heating your home even when renovating.
And, as well as being efficient and effective – offering a consistent heat throughout a room – it also offers aesthetic advantages such as freeing up wall space without the need for radiators.
However, with a variety of types available, how do you decide which is the best option for your particular project? Based on expert advice from Tim Pullen and those in the industry, we take a thorough look at underfloor heating so you can weigh up the pros, cons and understand which one best suits the needs of you and the construction of your home.
How does underfloor heating work?
Underfloor heating in either of its forms involves running a system of pipes or wires underneath the floor of a room. This effectively transforms the entire floor into one huge heat emitter that warms up the space.
Unlike radiators, which work by heating the air around them through convection, underfloor heating (UFH) uses both convection and radiant heat to warm a space. This combination of heating methods results in a consistent temperature which can be improved further by the addition of a good underfloor heating thermostat and and well-planned zones.
Heating from the ground up, also not only results in better comfort levels, but also puts less of a strain on your boiler when compared to traditional radiator systems. This is because of the lower operating temperature (around 40°C) of underfloor heating – radiator systems usually operate at around 65°C.
In fact, UFH is actually closer to being a ‘radiator’ than a radiator is. It heats the mass of the floor (the screed and the floor finish) and that heat then (mostly) radiates into the room – there is some convection going on but over 80% of heat transfer is by radiation.
It is also useful to note that underfloor heating is great when used in combination with renewable technology, such as heat pumps, which have a low flow rate.
Types of underfloor heating
There are two main types of underfloor heating:
- Wet underfloor heating
- Electric underfloor heating
In basic terms, a wet underfloor heating system features pipes, filled by warm water. Underfloor heating and boilers is one scenario, but underfloor heating with heat pumps is becoming an increasingly popular option. These pipes are typically embedded within a floor screed.
This is the best type of underfloor heating for those building from scratch and/or planning a whole-house system. However, there are also different types of wet underfloor heating depending on the type of floor you have and how it is constructed.
Wet underfloor heating: Your options
Wet underfloor heating comes in two different formats which means that asking how to install underfloor heating will give you two different answers, depending on whether you are building new, or relaying your floor from scratch.
- Buried underfloor heating: This system involves placing the pipes into the floor screed. The floor screed is finished, the pipes buried and the different zones are controlled by the underfloor heating manifold. This is the most efficient wet UFH system, but better suited to extensions and new builds where new floor screeds are required.
- Surface mounted underfloor heating: Also known as low profile systems, ths method involves specialist products that have warm water pipes installed in insulated panels. They are designed to be low profile, adding just 1.5cm to the floor level, making them more suitable for retro-fitting – as long as the increased floor level doesn't impact head space.
Electric underfloor heating: A good option for single rooms or retrofits
Wondering when you might need to consider electric underfloor heating instead? Simon Cook, head of sales at Nu-Heat explains that it generally comes down to the size and space you're looking to heat.
"Electric and wet underfloor heating systems are both great solutions when applied in the right scenarios," he says, "but while wet underfloor heating is an extremely efficient and effective whole house heating solution when paired with a bespoke design, it can require a larger upfront investment to install.
"Electric underfloor heating on the other hand is slightly cheaper to install, but far more costly to run. And, while it has a great response time, electric underfloor heating does lose heat a lot faster than warm water UFH. Therefore, it is best suited to small spaces such as kitchens or bathrooms."
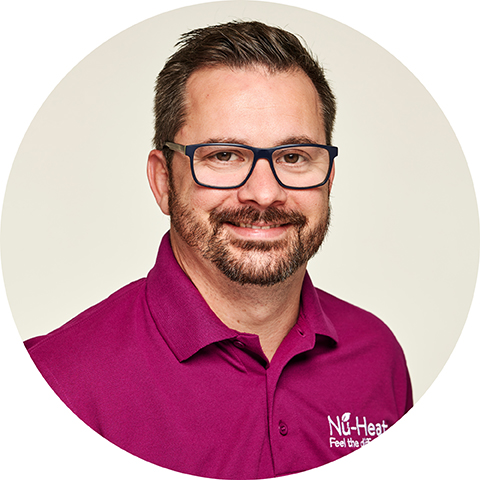
Simon Cook is Head of Sales at Nu-Heat and has spent 12 years with the company, gaining not just a vast array of knowledge, but also a sense of pride in working for a company that values its customers, reputation and products.
Underfloor heating controls
The majority of underfloor heating system controls feature two main parts:
- A digital zone control that determines the temperature of each room/area
- The underfloor heating manifolds and valves that the zone control operates
The zone control will be placed somewhere where the homeowner can make adjustments, while the underfloor heating manifolds will be placed out of the way – under the stairs or in a cupboard – so as to be unobtrusive.
There is no regular maintenance regime associated with underfloor heating, although knowing how to bleed underfloor heating can help ensure it's working to the best efficiency. If things do go wrong, it will typically be with the heating control systems rather than the system itself. In both electric and wet systems, you'll need to consider the best underfloor heating thermostats to make sure you have the required amount of control over your heating.
It's also important to understand what temperature underfloor heating should be set at to ensure you are getting the best out of your system and managing your energy as wisely as possible.
Pros and cons of underfloor heating
What are the advantages of underfloor heating?
Although underfloor heating is a popular option when self building, it can be harder to decide when it comes to choosing it for a renovation project or extension in a house that already has a radiator led system.
However, the experts say it's a matter that needs serious consideration when you way up radiators vs UFH.
"While most homes in the UK are still reliant on traditional radiator systems, they aren't the best solution for everyone," says Simon Cook. "Of course, a key advantage to radiators is that they are already installed in most homes and so are familiar to most and can be simple to upgrade.
"But, before you decide to stick with radiators though, there are some major drawbacks to consider," he suggests.
"Radiators heat through convection, and as well as this leading to uncomfortable cold spots and draughts, the air circulation can also worsen conditions for allergy sufferers by spreading dust and allergens, all while taking up valuable wall space," says Simon.
"In contrast, although underfloor heating can involve a higher initial investment and may require a slight adjustment period, it offers numerous benefits for health, efficiency, and comfort," he notes.
"Underfloor heating warms the room evenly from the floor up through radiant heat, making it 25% more efficient than radiators and up to 40% more efficient when combined with a heat pump.
"And of course, UFH saves valuable wall space as it is neatly concealed beneath the floor," he adds, "eliminating the design restrictions created by radiators, giving you complete design freedom."
Of course, each decision to install UFH or radiators will be dictated property by property, room by room, depending on heat loss and whether the output from an underfloor heating system is larger than this loss figure.
It's also worth noting that underfloor heating systems have a lifespan of 50 years plus, while the average radiator will only last between 8-12 years before becoming inefficient.
A wet underfloor heating system is estimated to be 25% cheaper to run than radiators when attached to a modern boiler and 40% cheaper when attached to a heat pump. Electric underfloor heating is believed to be around three times more expensive than wet systems however, as electricity is more expensive.
What are the cons of underfloor heating?
Of course there are also downsides of UFH to consider – particularly if you plan to retrofit underfloor heating.
- Underfloor heating is more expensive to install than a comparable radiator system
- Installation time can be longer, especially with wet UFH. Even electric underfloor heating may require work to self level before installation
- When retrofitting underfloor heating, changes to floor height will need to be considered. This may require extra work in digging out the floor for a level profile
- Not all floor coverings will work as well with UFH
Underfloor heating and renovations
In a new build, the extra cost of underfloor heating relative to the whole build cost is seldom a deal breaker.
However, if you're looking to retrofit underfloor heating in a renovation project, it can be disruptive and expensive as it often involves taking up floors that may otherwise be best left alone, or raising the floor level, which may have implications on the joinery (doors, skirting etc).
Low-profile systems tend to have smaller diameter pipes and run at a higher temperature. This means that the floor will heat up and cool down far more quickly than conventional underfloor heating.
Where underfloor heating is added to an existing radiator system then a different control system will be needed. Luckily, wireless underfloor heating thermostats (some of which can be controlled with a phone app) make installation far easier.
It is often a good idea to install electric underfloor heating in a small, single area like a bathroom or en suite, where it may be difficult to install wet underfloor heating.
It is worth noting that one of the most common – and worst – uses for electric underfloor heating is in a conservatory. Typically these areas need a lot of heat and are used for relatively long periods of the day (compared to a bathroom, for example). This means that running costs become an issue and the extra trouble and expense of a wet system may be well worthwhile.
Choosing the best flooring to use with underfloor heating
When it comes to choosing the best flooring for underfloor heating, there are a number of options available – some more suitable than others.
Although underfloor heating with tiles is one of the most popular combinations, there are pros and cons and specific requirements for other options such as UFH with laminate flooring and wooden flooring with underfloor heating.
Likewise, while underfloor heating with carpet can be considered, it won't be as efficient as when used with harder materials such as ceramic and porcelain tiles, luxury vinyl tiles and natural stone flooring.
Concrete is a superb heat conductor, so polished concrete floors also work really well with underfloor heating as the thermal mass of your concrete will retain heat and ensure your room stays warm for longer after your heating is switched off than would be the case with a radiator system. They are easy to pour over the pipework and they absorb and hold the heat produced well. Seek the advice of your installer before switching your underfloor heating on though – too soon and it could crack.
Most retailers will specify whether a flooring will work with underfloor heating, so look for that as your first guide when choosing what you will use to cover the floor.
FAQs
Should I leave underfloor heating on all the time?
Understanding how long does it take underfloor heating to warm up will help guide you towards the best way to run your heating.
With a wet system it can take two or three hours to warm up, so it is better to leave it turned on if you or your family are inside the house and need to keep warm.
To save costs, you can adjust the temperature instead, to make it lower during night time or times when you might not be using the space.
With electric underfloor heating meanwhile, the floor can heat up much quicker. The heating costs depend on how many kilowatts hours (kWh) of electricity you use and this will be more, the longer the heating is turned on or the more watts the underfloor heating uses. For a 125W system turned on for an hour, for example, this will use 1KWh for every eight square metres of electric underfloor heating
How thick should underfloor heating screed be?
The thickness of the floor screed during your installation process will make all the difference. The screed thickness in which the warm wet pipes sit will have a dramatic impact on how the system is used.
A thick screed will give a longer reaction time (the time taken to warm up and cool down), while a thin screed will have a quicker reaction time.
Which is right and best will depend on the construction of the house, your occupation habits and how the underfloor heating system is to be used, however, the following offers some guidance:
- If the pipes are housed in the concrete floor slab, this should be 150mm thick and give a reaction time of over four hours. In this situation, it is best to run the system all day, at a lower room temperature – say 15°C or 16°C – to provide background heating to the whole house. Highlight heating, such as a log burning stove, is a good idea in the rooms that are occupied
- A standard sand and cement screed would typically be 65mm to 75mm thick and the underfloor heating could take upwards of two hours to heat the room or cool down. This situation may be well-suited to rooms where we spend a lot of time, such as lounge or kitchen, but might be less acceptable in a guest bedroom
- With thinner flow screeds, we might expect a thickness of 35mm to 40mm and a reaction time of around 30 to 40 minutes – the system can be run in a similar way to a radiator system. Flow screeds offer better thermal conductivity than sand and cement, and being thinner and lighter means that they can be suitable for both renovations and new builds
How much does underfloor heating raise floor levels?
Underfloor heating will usually raise the profile of the floor. The amount it is raised by will depend on a number of factors such as how much insulation you need to add, pipe size, and whether you need a screed and floor finish.
There are also some products that get ‘carved’ into an existing screed, in which case there would be no additional build up other than the final floor finish.
If you want to retrofit a wet water system or have concerns about excavating or raising the floor, then low profile systems are a good option. "These have the advantage of coming in different heights and designs which allows them to be installed relatively quickly and easily on most substrates without impacting on the floor to ceiling height of the room," says Mark Dowdeswell, Senior Category Manager at Uponor.
Where should I buy underfloor heating?
Ultimately, the efficiency and success of an underfloor heating system will depend on the quality and design. Choosing a supplier who offers a good design service and aftercare is important. A specialist underfloor heating company is often best placed to achieve this.
If the design is wrong it is unlikely that the homeowner will know until they have lived in the house for a whole heating season – by which time it might be too late.
Finally, if you are choosing to pair underfloor heating with an air source heat pump or ground source heat pump, it is a good idea to choose one supply and install company. Both are complex systems and getting the whole heating system to work in perfect harmony is essential to a warm and toasty home.
Now you understand the basics of underfloor heating types and how it could work in your project, find out what you can expect to pay for underfloor heating costs, including installation and projected running costs.
Bring your dream home to life with expert advice, how to guides and design inspiration. Sign up for our newsletter and get two free tickets to a Homebuilding & Renovating Show near you.
Tim is an expert in sustainable building methods and energy efficiency in residential homes and writes on the subject for magazines and national newspapers. He is the author of The Sustainable Building Bible, Simply Sustainable Homes and Anaerobic Digestion - Making Biogas - Making Energy: The Earthscan Expert Guide.
His interest in renewable energy and sustainability was first inspired by visits to the Royal Festival Hall heat pump and the Edmonton heat-from-waste projects. In 1979
this initial burst of enthusiasm lead to him trying (and failing) to build a biogas digester to convert pig manure into fuel, at a Kent oast-house, his first conversion project.
Moving in 2002 to a small-holding in South Wales, providing as it did access to a wider range of natural resources, fanned his enthusiasm for sustainability. He went on to install renewable technology at the property, including biomass boiler and wind turbine.
He formally ran energy efficiency consultancy WeatherWorks and was a speaker and expert at the Homebuilding & Renovating Shows across the country.