Timber Frame Extensions: What You Need to Know
A timber frame extension can offer a more economical and sustainable approach to expanding your home. Here's what you need to know about these builds
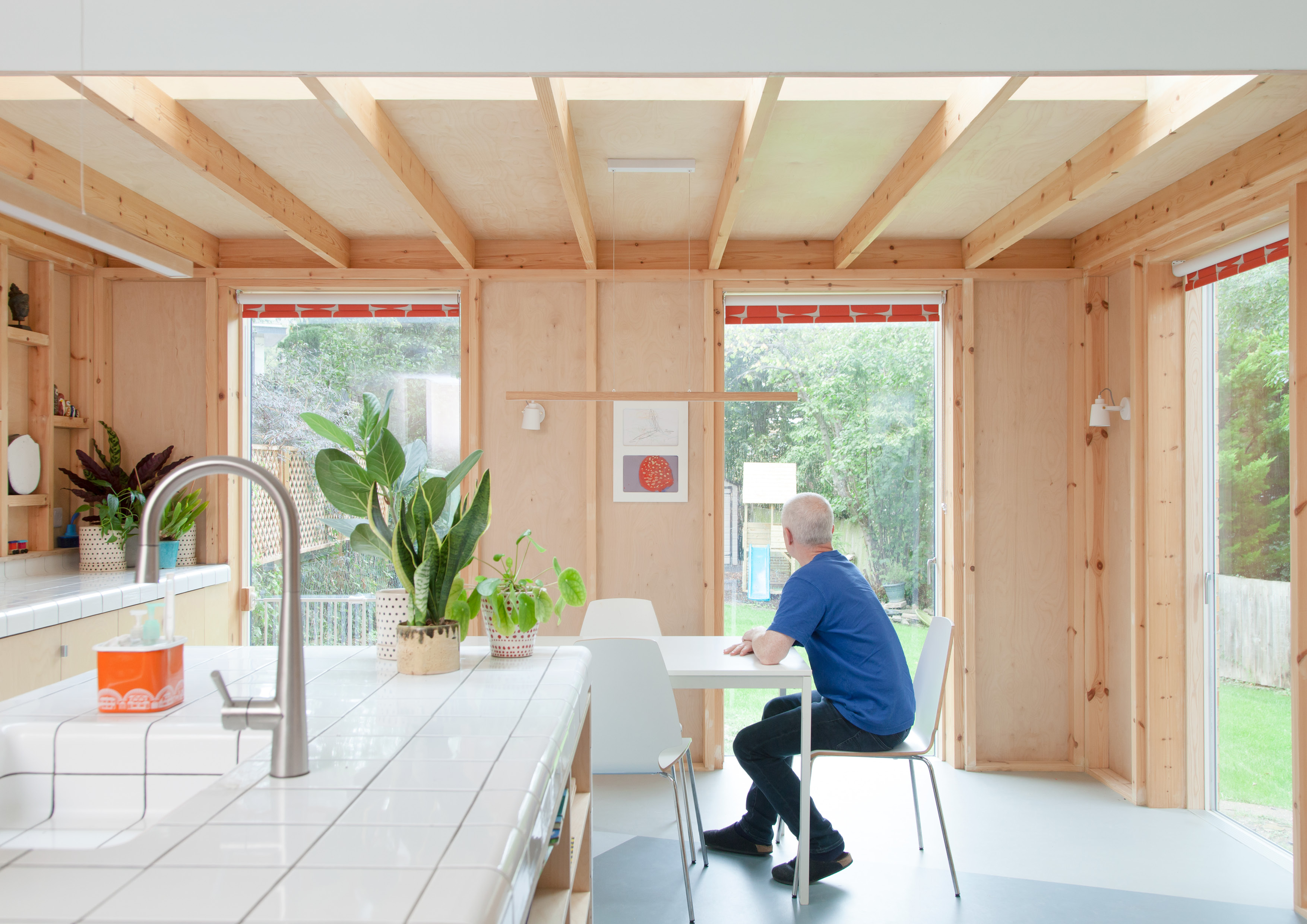
A timber frame extension is an impactful way to increase your home's space and add value to your property.
This type of extension is often quicker and easier to build than blockwork projects and is a great option if you're building on a budget.
Before you start your project, there's plenty to consider when using a timber frame method, from planning permission to how the frame is manufactured and what you clad it with.
Find out more about your options with our expert guide to timber frame extensions
Are Timber Frame Extensions Any Good?
There are many benefits to building a timber frame extension, and not just the extra space and added value that it gives to your home.
With a timber frame extension, you can achieve the weathertight stage in days rather than weeks, which not only means less time spent on site, but also less dependence on good weather conditions and reduced levels of disruption.
Once built, a timber frame extension can also offer good levels of thermal performance and airtightness, making it suitable for projects with sustainability at their core.
Is a Timber Frame Extension Cheaper to Build?
Generally, yes. The cost of a timber frame extension is accepted as being less than a traditionally-built extension primarily because there are fewer labour hours involved.
The timescale required to build it is also more predictable with it being less dependent on good weather conditions, particularly if the works are being carried out in the winter months.
(MORE: Extension Cost Calculator)
If you propose to take out or increase a current mortgage to help pay for the extension you should always check with the lender what external finish is acceptable to them, some are very conservative on what external finish they will accept which may limit your choice of lenders.
Also, with any home improvement or extension project, remember it should add more value to your house than it costs to undertake the work.
Do I Need Planning Permission for a Timber Frame Extension?
Not necessarily. If your proposed extension meets certain criteria in terms of size and position, then you may be able to extend under Permitted Development Rights (PD). If you want to build something outside of the scope of PD, then you will need planning permission.
Always double check with your local authority before starting work, especially if your property is listed or located in a conservation area or Area of Outstanding Natural Beauty.
(MORE: Read our guide to planning permission)
Is a Timber Frame Extension Built On Site?
The vast majority of extensions built using timber frame are ‘stick build’ – this is where the timber frame panels are made up on site by the joiner as opposed to being manufactured in a factory.
A structural engineer would design the timber frame and prepare a specification of the size/grade of timbers to be used for the frame/lintels/cripple studs and so on, together with a nailing schedule.
The joiner would take delivery of all the timbers required and as they are loose they can easily be man handled through restricted access areas to where the panels are to be made up.
The joiner would then make up the timber frame panels on site following the structural engineer’s specifications and because the existing structure would be opened up/exposed at this point it allows him to take accurate dimensions and manufacture the panels to suit.
If your chosen design features large expanses of glazing then a steel or glulam portal frame/goal post arrangement may be required (a structural engineer would advise on this aspect). This can be fabricated off-site, delivered in sections and bolted together on site.
(MORE: Guide to building a single storey extension)
If any part of the extension is below finished ground level then timber frame construction would not be suitable for that element of the build.
You may find that manufacturers are reluctant to quote for extension projects as they require a lot more technical input when compared to a new build. Very accurate site dimensions have to be provided for an extension to make sure the likes of floor levels, eaves and roofs line through with the existing house.
It is sometimes nigh impossible to obtain accurate manufacturing dimensions until elements of the existing house can be opened up/exposed to establish exactly how it was originally constructed. That can cause considerable delays as most manufacturers will have a lead-in time of at least 6-8 weeks from having all the information they require prior to the delivery date.
Manufacturers may also be put off providing a quote if site access is very restrictive. And, with the typical single storey extension of say 3.6 x 4.8m only requiring a part load, it makes the transportation costs uneconomic when compared to ‘stick build’.
Which Exterior Finish Works Best on a Timber Frame Extension?
The timber frame extension can be finished externally in a variety of materials, including:
- Facing brick
- Rendered brickwork/blockwork
- Natural stone
- Reconstituted stone
- Brick slips
- Timber
- Fibre cement cladding
- Metal cladding
- Render board system
But, if being built on a boundary then the external finish has to be non-combustible and provide a minimum one hour’s fire resistance to satisfy Building Regulations.
Top Tips for Building a Timber Frame Extension
- Choose a designer with experience in designing timber frame extensions
- Get three detailed quotes and go over them with your designer to ensure you are comparing on a like for like basis
- Always have a contingency budget of around 10% to deal with any unforeseen circumstances
- Don’t forget to budget for external works including paving, decking and landscaping
Factoring in a Movement Gap for a Timber Frame Extension
Where any extension (irrespective of the construction method used) is attached to the existing building it is very important to ensure a movement gap is formed to accommodate shrinkage, thermal and moisture movement.
The extension will most likely be a different construction to that of the existing building and as such will expand/contract at a different rate to the existing building, hence the requirement for a movement joint.
Movement joints are typically formed by using a stainless steel channel tie system which provides lateral restraint but allows for both horizontal and vertical movement, the gap formed between the two structures is filled with a flexible sealant (different colours are available) to make it weathertight.
Bring your dream home to life with expert advice, how to guides and design inspiration. Sign up for our newsletter and get two free tickets to a Homebuilding & Renovating Show near you.
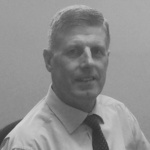
Mike is an expert in self build, with a particular focus on timber frame construction, and offers advice on the build process as well as the cost elements of building with timber. He has been in the industry for 47 years. He set up his own architectural consultancy in 1985, focusing on extensions and individual new builds, before joining Scotframe, a leading timber frame supplier, between 1991 and 2017. He now runs his own self-build consultancy. As well as helping hundreds of self builders realise their dream homes, he has also presented to the Scottish Government regarding the importance of self build, and has been the deputy chairman of the Structural Timber Association's (STA) self-build committee. He has also self-built twice.