Oak Frame: Is it the Right Construction System for Your Build?
Our complete guide to oak frame projects looks at the pros, cons, cost implications and other key considerations when building with oak
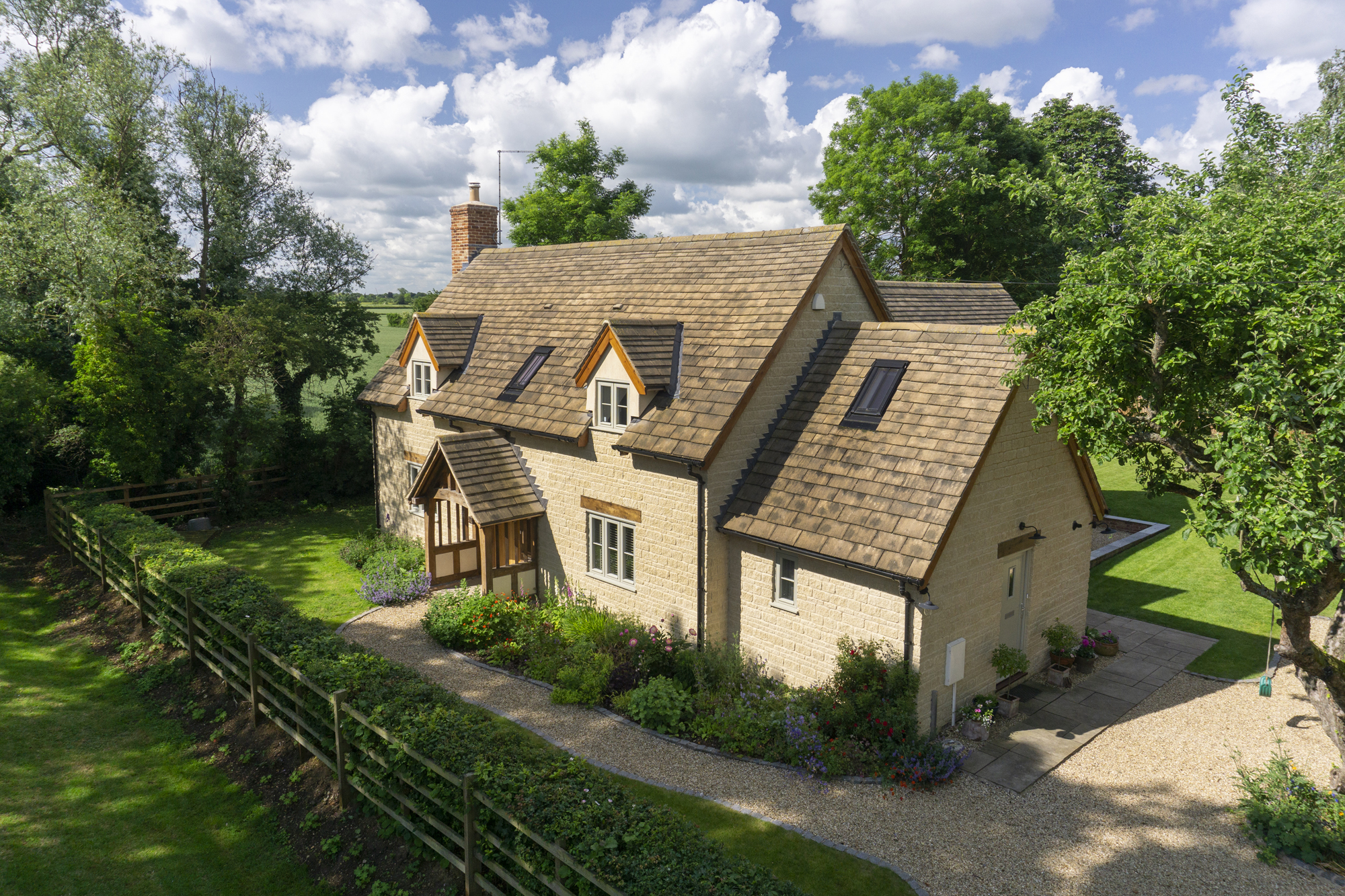
Building with oak frame is a popular choice for self builds, not least of all for the character exposed beams can bring to a new property. While oak frame is often viewed as being used for homes with a more traditional style, you don't have to look far to find some incredible examples of modern homes built using oak frame too.
(MORE: Ideas for Oak Frame Homes)
As well as the handsome, tactile nature of oak, it's a naturally strong and durable material.
If you're considering oak frame for your project, read on for our complete guide with everything you need to know — from how much it costs, whether its sustainable and the types available. Plus, we dispel some common myths about oak frame houses.
Types of Oak Frame
You have several options of oak frame for your project which can contribute to either a modern or traditional finish. This is largely led by your choice of hidden or exposed frame.
Exposed Oak Frames
The principal characteristic of an exposed oak frame is that the oak is (usually) exposed both internally and externally.
Internally, the principal walls, floor joists, trusses and roof members can all be visible. Between the exposed oak timbers are the render panels. These consist of extremely thermally-efficient foam panels fixed to board and set within the panel timbers.
Bring your dream home to life with expert advice, how to guides and design inspiration. Sign up for our newsletter and get two free tickets to a Homebuilding & Renovating Show near you.
Hidden Oak Frames
Hidden oak frame houses are usually based on a heavy oak frame, although it could be Douglas fir, and they invariably have a more open feel to the structure. They are a perfect match for large glazed areas.
External finishes can be a combination of infill panel insulation, external cladding and large scale glazing.
Fully vaulted roofs are a feature of this design creating a spacious feel. A major attraction of this style is the flexibility it allows in design and usage.
Pros and Cons of Oak Frame
Benefits of Building with Oak Frame
- Oak is naturally resistant to insect and fungal attack
- Impervious to weather
- Virtually maintenance free
- Increases in beauty and strength with age
- Can be sustainably sourced
- Work well on sloping sites
Drawbacks of Building with Oak Frame
- Requirement to design around beams
- Limit to room's open depth without encountering a post of around 4.5m
- Oak frame can be difficult to light well internally
Cost
How Much Does an Oak Frame Cost?
Building with oak frame is a premium option and people don't build oak frame houses to save money.
Oak is one of the most expensive timbers you can use. Oak framed homes tend to cost in the region of £1,696 – 2,120 per m², although it’s possible to build one for as little as £1,000/m².
There are multiple ways to make savings or splash out on high-end features, but you can expect the cost of the frame to be between 18-33% of the total build cost.
- A guide figure would be £20-£45 per square foot for the skeletal frame design, fabrication and erection
- With regard to budgeting for a full build, the cost averages at approximately £160-200 per square foot (£1696–2120 per square metre)
- If you are planning to manage the project yourself using local tradesmen rather than a main contractor you can save 15-20%
- If you decide to undertake some of the work yourself there is scope to make further savings – potentially the full cost of labour if you have the time and skill, amounting to 50%.
Is It Possible to Build With Oak Frame on a Budget?
Post and beam homes in other countries rarely use oak. In North America, they usually use Douglas fir or some other softwood species, and there is no reason why you can’t use something cheaper than oak.
Where oak really comes into its own is in large open plan spaces, especially ones with vaulted ceilings. There is nothing to stop you going for a conventionally built home and adding an oak framed extension, enabling you to get the ‘wow factor’ on a budget.
Is Building with an Oak Frame Sustainable?
Where Does the Wood for Oak Frame Come From?
Almost all of the oak used in British green oak homes is sourced from sustainable plantations in France and Germany, with companies replanting many trees to compensate.
English oak is available but it’s more expensive and it tends not to grow so tall and straight, which makes it more suitable for furniture than construction. The species is identical.
Oak trees are harvested when they are around 80 years old. Each one will produce roughly 15ft³ of construction-grade oak. The typical oak-built family home uses 800ft³ of oak — the produce of around 50 trees.
The term green oak refers to newly-felled timber because it has a high moisture content and it’s much easier to work. With oak, you have to work it in its green state because, after four or five years, it becomes so hard that you can no longer cut or machine it.
Much of the skill in working with green oak is to know how the timber will shrink and to make the joints so that they get tighter as the timber hardens.
Can I Build an Eco Home Using Oak Frame?
There are a number of areas where an oak framed house can deliver on those all important eco-credentials.
Airtightness is essential to creating an energy-efficient home. Airtightness refers to the infiltration of cold/hot air into the building and/or the loss of heated/cooled air from inside through gaps, cracks, holes, etc in the building fabric.
A key factor of airtightness is your choice of insulation. It’s likely that your oak frame supplier will have various insulation systems to offer, which differ in cost and performance.
There may also be some technology that allows for the natural changes in size of the oak frame through the seasons. Some systems are delivered in a cassette format, slotting in to walls, floors and ceilings in a way that fits together in order to maximize airtightness.
You could integrate solar panels to produce hot water and/or electricity, or consider installing a heat pump which operates well with low-heat-demand heating systems such as underfloor heating.
Common Misconceptions of Oak Frame
Does Oak Frame Shrink?
Yes, during its first few years, oak shrinks by as much as 5% radially (that is across the grain), but the length of each piece remains the same. If you work with a good designer, they will this into consideration when putting frames together, so it's no cause for concern.
However, when detailing the joints connecting the posts and beams, the shrinkage factor is used to make the joints tight. The pegs used to fix the joints are always tapered and the holes between the timber are normally offset, allowing the shrinkage to gradually draw them into a strong alignment over time.
Another area where shrinkage is a factor is glazing and joinery. Oak builders have become adept at designing weatherproofing details which can cope with a backing frame which is set to shrink.
Is an Oak Frame Home More Likely to Burn Down?
No. Structural timber is, in fact, not quick to burn. Research shows that fire fighters would rather enter a timber frame building on fire as timber has a known and predictable burn and char rate. Plus, it is not explosive.
All timber frames commercially available have to be manufactured and erected in accordance with all regulations and warranties. Lenders and insurance companies do not differentiate between timber frame and masonry construction.
Finding a Supplier
How Do I Find an Oak Frame Supplier?
All oak framed housebuilders offer a bespoke service. Some are very small, little more than one-man bands, whilst others are now well established as design and build businesses, catering mostly to the self build market.
If you have decided that an oak frame house is for you, what should you be looking for when it comes to choosing a supplier?
- Look for a company that can produce the type of home you want, by looking at their brochures and website
- Try and visit their finished houses in person
- Check the company is reputable with a solid trading history
- Find out what the payment terms are. How much will you need to pay as an upfront deposit? How will your money be held?
- Choose a company with plenty of experience of building timber frame post and beam and working with self builders
- It is essential that you get on well with them and they have an understanding of your project.
Perhaps the biggest difference between suppliers is whether they use machine cutting or stay with traditional handmade work. Computer-controlled cutters are faster and potentially more accurate, but they usually require the oak to be planed beforehand, which gives the wood a rather different look. On the other hand, machine cutting can sometimes achieve levels of complexity which would not be easy to replicate traditionally.
The designs can also vary from traditional, Tudor-style farm houses and cottages to stunningly contemporary, open plan homes, with lots of built-in glazing. Some businesses specialise, others are happy to work in any style.
Mark is the author of the ever-popular Housebuilder’s Bible and an experienced builder. The Housebuilder’s Bible is the go-to hardback for self builders; originally published in 1994, it is updated every two years with up-to-date build costs and information on planning and building regulations, and is currently in its 14th reiteration.
He has written for publications such as Homebuilding & Renovating for over three decades. An experienced self builder, his latest self build, a contemporary eco home built to Passivhaus principles, was created on a tight urban brownfield plot.