Which floor structure is best for your home?
The methods used to construct new floor structures have come on hugely in recent years. Chartered surveyor Ian Rock offers a self-builder’s guide to getting the ground under your feet structurally sound
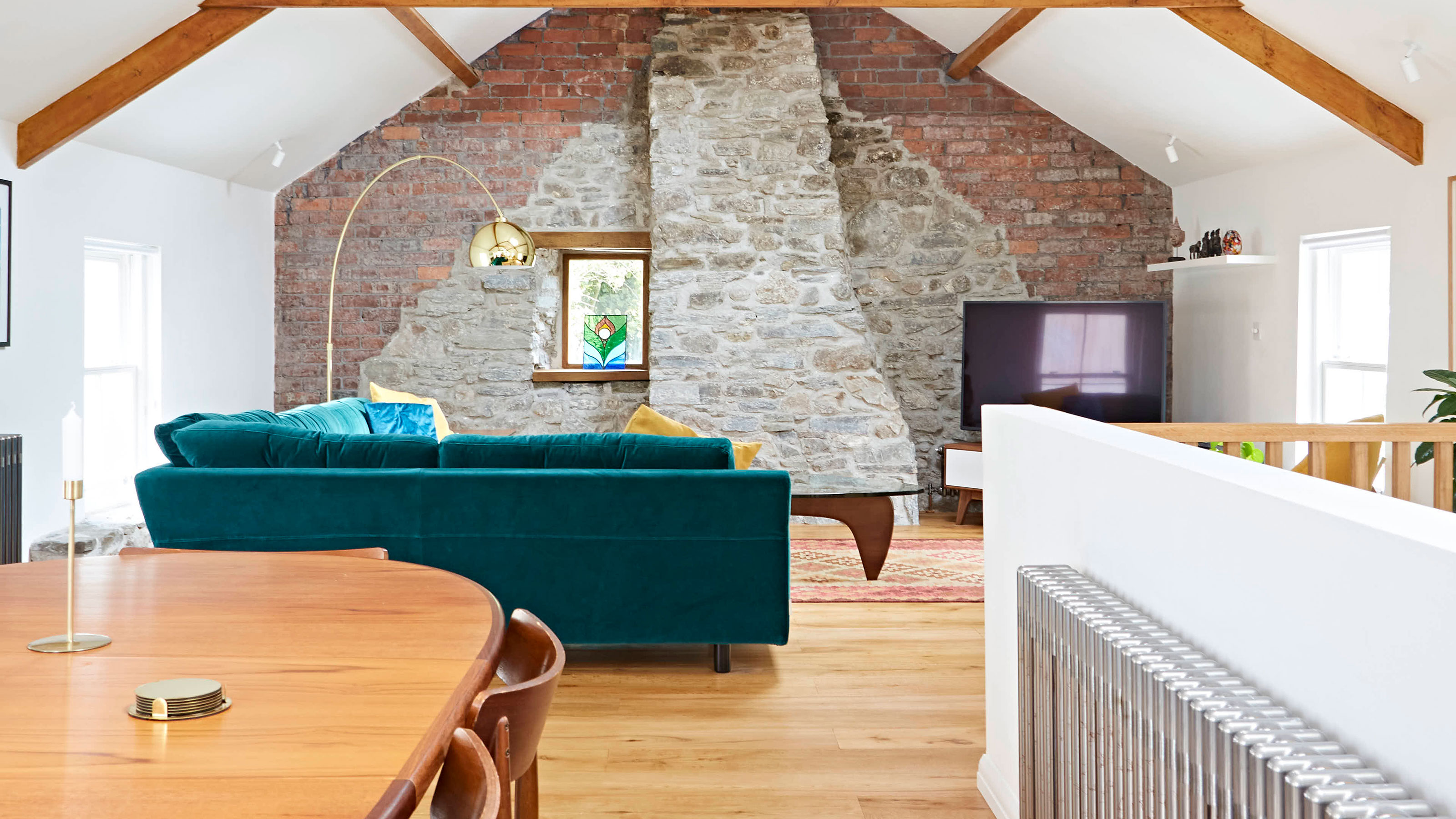
Few things are as important in any homebuilding project as ensuring the floor structure under your feet is stable, level and generally fit for purpose.
Unless floor structures are carefully designed early on in your self build, you could end up with uneven, sloping or springy floors in need of expensive remedial work. So before finalising your design it’s worth taking a look at the main options for floor construction and how the choices you make can have an important impact on the rest of the build.
At the dawn of the new millennium, many new homes were still being built to a formula little changed since the Victorian era, with solid concrete slabs downstairs and boarded 8x2inch timber joists ‘up top’. But both types suffered from significant drawbacks.
Timber floors were constrained by stunted spans and prone to developing draughty gaps and annoying squeaks; their intolerance to damp also rendered them vulnerable to attack from fungal decay and beetles. Concrete slabs fared little better, with a tendency to sink and crack over time, and a propensity to conduct cold into the home.
Fortunately, in the intervening years, technology has leapt ahead, transforming the options available to domestic buildings. Here, we explore the options available for both ground and first floors and the most important considerations to mull over before deciding on the right option for you.
What type of floor structures are there?
The positioning of the upper floors will dictate how much residual headroom you have in the rooms below. Therefore it’s essential at the design stage to factor in the full depth of the floor structures — including boardings and coverings, ceilings and plasterwork.
It’s equally important to calculate the finished surface height of ground floors once fully insulated and screeded with floor coverings in place. There can be additional challenges when building an extension as floor levels need to be aligned so you don’t end up with awkward steps between the main house and the new accommodation. Detailed section drawings are invaluable for assessing the available vertical space, bearing in mind that there may be planning restrictions on roof heights that can potentially constrain the dimensions of top-floor rooms.
Another factor that can easily get overlooked at the design stage is the need to accommodate pipework and ducting for ventilation, heating and hot water systems within new floors. There are several different types of floor structure that are used the most commonly in the UK, including:
- Beam and block floors are the most popular solution when building a ground floor on self build sites. Concrete slabs are a good alternative for small extensions (where beam and block floors are uneconomic)
- Beam and block systems which utilise insulated blocks can provide an even quicker installation
- Solutions for first floors include traditional softwood joists, timber I-joists or open metal web joists; the latter options are more expensive but provide considerable benefits. Unlike softwood joists, timber I-joists do not warp over time, providing a ‘quiet floor’, while open metal web joists can provide an easy means of installing services
How do building regulations affect floor structures?
The primary role of any floor is to safely support the loadings imposed by occupants, fittings, furniture and so on. But floors also play a key role strengthening the overall structure of the building, helping to tie in the main walls and support internal partition walls.
Drawings for Building Regulations applications will need to show how the floor structures themselves are supported as well as demonstrating how loadings are transmitted down to the foundations.
Building control will also want to see structural engineer’s calculations to prove joists are of sufficient strength for the specified spans. Compliance with Building Regs additionally extends to areas such as fire safety as well as thermal and sound insulation.
Are beam and block ground floors always the best option?
Reinforced concrete beams infilled with blocks are a comparatively recent method of ground-floor construction.
Pre-cast beams are laid in rows in a similar fashion to traditional timber joists and the spaces between the beams are infilled with concrete blocks. Flooring grade insulation is then placed over a DPM and the floor is given a screed finish. Standard concrete beams can typically span about six metres without support from sub-floor walls.
It’s essential that the void under the floor (which should be at least 150mm deep) is vented via airbricks in the lower walls to protect the building from any build up of noxious gases such as radon or methane. On this note, you may be required to install a radon barrier and sump too by Building Control. The void can also provide a handy place to run service pipes.
One slightly odd quirk with these floors is their slight upward camber (more than 10mm over a 4m span). This isn’t a problem with a conventional screed finish, but with dry floors (such as ‘floating’ insulated chipboard panels) a self-levelling compound may first need to be applied.
Suspended concrete flooring systems were originally developed as a means of overcoming ground problems such as unstable sloping sites, where it made sense to bridge deep gaps rather than fill them. Today, nearly all new houses employ beam and block construction for their ground floors. Although the cost of materials is relatively high, ground preparation is minimal and a beam and block floor is quick to install, with significant savings in labour.
Specialist suppliers can custom design beams if supplied with a set of approved drawings, or they can be ordered via builders’ merchants.
The main drawback with beam and block floors is that they are uneconomic below about 50m2 — so they are not a solution for small extensions. It’s also important to note that the heavy weight of longer span beams requires use of a small crane to lift them into place. Therefore, they are best suited to larger projects such as new builds.
On the positive side, unlike timber floors, suspended concrete doesn’t shrink, creak or bounce. This makes the system well-suited for upper floors which need to be exceptionally strong.
They are best for larger projects such as new builds and upper and ground floors where a greater degree of strength is required
How do you insulate beam and block floors?
Insulating floors is always important and when it comes to suspended concrete floors it is essential that they are properly insulated from blasts of cold air blowing through the subfloor void underneath your feet. The Building Regulations’ ‘backstop’ target U value for ground floors is 0.25W/m2K, which should be easily achievable with 75mm or 100mm-thick rigid insulation boards laid over the surface.
Polyurethane (PUR) is a more effective insulator than expanded polystyrene (EPS), meaning a thinner board can be laid to achieve the same results. The insulation can then be covered with a conventional wet sand/cement screed of approximately 65mm thick, or with a dry floating chipboard deck. Alternatively, a highly insulated composite ‘floating floor’ finish can be applied using special panels made from insulant material bonded to a base of either plywood or chipboard laid over a polythene vapour barrier.
However, the most efficient solution combines two layers in one — minimising the depth of the floor by making use of the wasted space in the void below. Rather than adding an extra layer of insulation above standard blockwork, the insulation is incorporated into the structure. Systems such as Jetfloor, Litecast XT and TETRiS use special insulated polystyrene infill panels between and beneath the floor beams, helping to eliminate cold bridging. You can read more about cold bridging, also known as thermal bridging, in our piece on 'what is a thermal bridge'.
What do I need to know about beam and block floors?
- The pre-cast reinforced concrete beams are laid in rows in a similar fashion to traditional timber joists, with their ends resting on the inner leaf of the main walls over the damp-proof course (DPC).
- Their inverted T profile is designed to accommodate standard 100mm deep concrete blocks (which are typically 440mm wide), making infilling between the rows remarkably quick and inexpensive.
- Standard beams are 150mm deep, although for longer spans deeper 225mm sizes are available.
- For greater strength the rows can be laid closer together with the blocks instead laid sideways. The floor surface is then stabilised by grouting with a weak sand/cement mix brushed into the joints.
What is the quickest type of floor structure to construct?
The quickest way to construct an entire floor is by craning in enormous ready-made hollow core concrete flooring planks. These feature a hollowed-out interior to reduce their weight.
Inevitably the price you pay for super-swift buildability is the relatively high upfront cost, but the system also offers potential savings in terms of flexibility in the location of internal walls, which can be built on top without the need for additional support. Hollow core decks are used mainly for upper floors in flats, but are ideal for cantilevered balconies, although cold bridging can be a potential design issue.
What are the pros and cons of solid concrete floors?
Ground floors built of solid concrete remain popular with small builders and can often be an economic solution for home extensions.
Solid concrete ground floors have the twin advantages of being comparatively cheap and straightforward to build. Construction starts with clearance of the oversite ‘footprint’ before a thick base layer of clean hardcore is laid and firmly compacted into the ground. Once levelled with a layer of sand the hardcore base is covered with a damp-proof membrane (DPM) ready for the floor slab to be poured from a ready-mix concrete wagon.
Slabs rely on careful ground preparation and a well-compacted hardcore base. Unfortunately, this often gets skimped on site with the result that slabs can start to sink years later, leaving a cracked, hollow surface.As a precaution against cracking, concrete slabs are sometimes strengthened by incorporating sheets of steel mesh. Insulation boards can either be placed on top of the DPM or above the concrete slab. A screed finish is then usually applied over the floor structure to form a level surface.
But there’s a risk with solid slabs. Whereas foundations are normally dug down at least a metre to anchor the building into solid ground, floor slabs sit on the cleared oversite, less than half a metre deep. So this isn’t ideal on soils prone to seasonal movement, like shrinkable clay with trees in the vicinity.
It’s also important that hardcore is specified as ‘clean’ — old demolition rubble containing lumps of plaster and wood can hold moisture or start to rot. Worse still, chemical reactions in poor-quality hardcore can cause solid floors to expand, bulge and crack. However, despite such risks, when laid correctly this method can be a cost-effective solution — be sure to familiarise yourself with the process of insulating concrete floors too.
How are solid concrete floors installed?
Solid concrete floors are typically built in six layers (plus two more if you include underfloor heating and the floor coverings). The key stages are:
- The oversite area is stripped of vegetation and topsoil. Then a base of clean hardcore at least 100mm thick is laid. The ideal material for this purpose is a loose granular sub-base such as MOT Type 1, which can be delivered to site. Being largely self-compacting, this only requires a quick going over with a hired wacker plate before levelling with a layer of sand blinding.
- To prevent any dampness percolating through, a 1,200 gauge plastic sheet damp-proof membrane (DPM) is placed over the sand blinding, or alternatively laid higher up on top of the concrete slab. Either way, the edges must be joined up with the DPC (damp-proof course) in the walls. It’s common for flooring-grade rigid insulation boards (e.g. PUR) to be placed on top of the DPM at this stage, in thicknesses ranging from 50mm to 100mm.
- The DPM must be lapped up around the edges of the slab and screed to protect against cold bridging and also around incoming water pipes and soil stacks, etc. Alternatively, the insulation can later be placed on top of the concrete slab prior to screeding.
- The slab is normally at least 100mm thick, cast from ready-mixed concrete (a relatively strong mix). The fresh concrete needs to be ‘tamped’ as it’s poured to remove air bubbles and excess water. Depending on ground conditions, the slab may need strengthening with steel mesh or special fabric reinforcement.
- It takes two or three days for concrete to cure and in cold weather it needs to be protected with suitable sacking or old carpet. In hot weather, concrete can also be vulnerable to drying out and cracking, requiring a periodic light sprinkling of water. Concrete should not be poured when temperatures are below about 5°C.
- Instead of finishing the slab with a conventional screed, it’s perfectly feasible to level the surface of the slab with a power floater, which results in a hard-wearing floor finish. Insulation will need to be added below the slab in this instance.
What are the differences between floor structures for ground floors and first floors?
Perhaps the most striking difference between upper and lower floor levels is the greater risk of damp and rot at ground level. This may explain why traditional timber ground floors were largely superseded in the early part of the last century by more robust concrete slabs.
One obvious advantage with ground floors is there’s a readily available means of support via sub-floor brick piers or dwarf ‘sleeper walls’, although these need to be built with suitably deep foundations. For upstairs floors, which are mostly of timber construction, support from internal walls or beams is likely to be required, potentially complicating interior layouts.
Timber floors may largely be a thing of the past downstairs but they still enjoy a virtual monopoly upstairs.
How are suspended timber floors constructed?
Suspended timber floors are constructed from a series of parallel joists clad with chipboard panels, pine floorboards or plywood sheets. Traditionally, joists were cut from lengths of 8” x 2” softwood, but today, to comply with Building Regulations, joist sizes, spans and spacings must be determined by reference to published span tables.
The basic method of construction is the same for both ground and upper floors, although with ground floors it’s essential that the subfloor voids are well ventilated via airbricks so any dampness can evaporate. To prevent joists deflecting they need to be braced with strutting or noggins wedged in between. Steel straps also help prevent movement by tying joists to the main walls.
Kiln-dried softwood joists typically span up to about 4.5m between structural walls or steel beams. Joist ends must be supported from galvanised steel joist hangers rather than simply being embedded within the walls.
Softwood joists are available in standard sizes such as 38x225mm and their spacing determined by published span tables, usually at 400mm, 450mm or 600mm centres. To support partition walls and accommodate openings for staircases, for instance, the rule of thumb is for joists to be ‘doubled up’, although building control will want to see the structural engineer’s calculations to confirm adequacy.
To prevent joists deflecting and wobbling about, bracing in the form of herringbone strutting needs to be inserted between the joists, usually comprising purpose-made steel X struts and wooden noggin offcuts. Steel straps also help prevent movement by tying floors to the main walls. The enduring popularity of timber floors is probably down to the fact that they’re a relatively inexpensive option as well as being straightforward to build and easy to adapt on site.
Traditional pine boards cost about twice the price of chipboard (which must be of a moisture-resistant type), but are hard to beat for natural appeal. Timber is also the most sustainable option but has a tendency to suffer from shrinkage resulting in floors becoming squeaky over time, and is always potentially vulnerable to subsequent weakening from careless notching and drilling for pipe and cable runs.
What are timber I-joists?
Factory-made timber ‘I-joists’ are now the predominant form of upper-floor construction in most housing developments — they are also commonly used in flat roof extensions. These are similar in appearance to RSJs with top and bottom flanges made of softwood or laminated veneer timber (LVL) bonded to a vertical web of oriented strand board (OSB) or similar engineered board. Being both strong and lightweight, manufactured I-joists can span six metres or more without support from internal walls or beams. Like their softwood cousins, they can be cut to length on site and the webs can be drilled to accommodate pipes and cables, but they can be installed in half the time, making them a popular choice.
Their main appeal is that, being strong and lightweight, they can span 6m or more, without support from internal walls or beams.
While they cost roughly twice as much as standard softwood joists, they be installed in half the time. Their superior rigidity and strength-to-weight ratio makes for easier handling, and they typically feature pre-formed knock-out panels designed for pipes and cables to be threaded through. They can be cut to length and the webs can be drilled, but the top and bottom flanges must not be cut. To provide lateral support, ‘blocking panels’ made from strips of engineered wood or spare I-joist offcuts are wedged between the joist ends.
There’s another reason why I-joists have captured the hearts of developers, self builders and renovators alike — unlike standard softwood joists, I-joists aren’t prone to shrinking and warping, making them perfect for ‘quiet floors’. It’s even claimed that some products do not require sound insulation when installed at 400mm centres or closer.
Timber I-joists are a popular alternative to softwood joists due to their stability (they’re not prone to warping, so provide a ‘quiet floor’) and ability to span greater widths. The webs can be drilled to accommodate services, but can also be specified with pre-formed knock-out holes for this purpose
How do open metal web joists work?
Open web joists are an alternative type of engineered flooring solution, marketed under a variety of brand names such as ‘Eco-joists’. Like I-joists they have a top and bottom flange but are held together by a lightweight wavy central steel web. They are relatively expensive (they typically cost about 10 per cent more than timber I-joists) but are extremely strong yet remarkably light and capable of achieving unrestricted spans up to about eight metres. Installation time is around half that for the traditional softwood variety, plus there’s no need for bracing, which helps keep labour costs in check.
They come in a range of depths, from 195mm to 304mm, and can be hung from the top or the bottom chord. The installation time is claimed to be around half that for the traditional softwood variety, plus there’s no need for bracing, which helps to reduce labour costs. Like I-joists they have the benefit of resisting shrinkage-related problems.
Because the whole system is open, they can accommodate bulky service runs such as mechanical ventilation ducting and full bore 100mm waste pipes, although where different lengths run alongside each other you need to check the webs all line up. The main drawback – apart from the cost – is that they need to be custom made to suit the dimensions of your build and can’t be cut on site to fit, although some suppliers incorporate adjustable ends for minor trimming.
Which floor structure should you choose?
Solid concrete ground floors are well suited to smaller home extension projects. Although the work is labour-intensive the relatively cheap cost of materials makes this method popular with small builders and DIYers on a budget. But for more sizeable extensions and new homes, beam and block ground floors have now largely eclipsed solid concrete. This method can also be an effective solution on sites where the ground is prone to seasonal movement or is potentially unstable. Although prefabricated concrete beams are relatively expensive to buy, infilling between the rows of beams with standard concrete blocks makes this part of the job quick and inexpensive; plus there’s a lot less ground preparation.
Beam and block can also be used for upper floors in buildings where strength and stability is key, such as flats. Traditional timber, however, is the default method for upper-floor construction as it offers the significant advantages of being relatively inexpensive and straightforward to build on site. The main downside with conventional softwood construction is the tendency to suffer from shrinkage resulting in floors becoming squeaky over time, hence the appeal of I-joists and metal web joists despite costing around twice the price
of equivalent softwood.
What is the best way to weave in services?
One of the biggest dangers with floor structures is the weakening and instability caused by careless subsequent cutting of joists for pipe and cable runs. So it’s important that suitable pathways are planned at the design stage to avoid any risk of compromising the structural integrity of joists, or ending up with ugly surface-run waste pipes, ventilation systems and so on. The job of weaving pipework, ducting and cabling through floors normally takes place at first fix stage soon after floor joists are installed but before the undersides are lined with plasterboard to form the ceilings.
To avoid the need for cutting notches into joists most plumbers now use long lengths of flexible plastic pipes to supply heating and hot and cold water which can be threaded in a similar manner to electric cables through small holes drilled centrally in joist webs. Better still, open web joists are purpose made to accept even large bore pipework without any cutting or drilling. If all else fails, constructing a separate false suspended ceiling below the main structure can be a good option. This can provide a very useful space for concealing large amounts of ducting, conduit, pipework and lighting cables, as well as allowing holes to be cut for recessed lighting without risk of compromising soundproofing and airtightness.
How do you sound proof floors?
Building Regulations require ground floors to be thermally insulated, which typically involves laying thick sheets of flooring-grade insulation over the floor structure prior to screeding. With suspended timber floors this is more of a challenge because fitting insulation between joists adds significantly to the cost and complexity of the job. With upstairs floors thermal insulation is only necessary where rooms are located directly above cold spaces such as garages. Part E of the Building Regulations does, however, require floors to be insulated for sound, and this can usually be achieved by packing sound-absorbent mineral wool between joists or by laying special acoustic flooring
In terms of soundproofing and noise control, special acoustic flooring, such as pre-insulated chipboard panels, can be used to build a sound-deadening floating floor. Other methods include fixing ‘resilient bars’ to the undersides of joists prior to plasterboarding; British Gypsum’s Gypframe RB1 Resilient Bars is one such product.
Where resistance to the passage of sound is a particular design factor, suspended concrete flooring is normally the best solution. There are systems such as the beam and pot system from Litecast that can achieve exceptionally high performance with specially formulated ‘robust tray tiles’ between the concrete beams. Whatever your choice of flooring, it’s obviously best to avoid cutting holes in ceilings for recessed lighting; a better idea is to construct a false suspended ceiling underneath to run ducting and lighting.
Who will construct the floor structure?
Construction of ground floors starts at the initial groundwork stage when the oversite area is cleared of topsoil. Once the lower main walls are built up to damp proof course level, work can begin installing floor beams or compacting the hardcore base for solid concrete floors. No specific trade is tasked with this role so it may be undertaken by a combined force of labourers, brickies or groundworkers.
The construction of timber floors normally has to wait until the building is watertight. Once the main walls are erected and roofs covered the carpenters can start preparing and installing joists into steel joist hangers. In the meantime, large sheets of plywood decking can be laid over the floor skeleton to serve as a temporary work platform until it’s ready for boarding.
How much do different floor structures cost?
Of the common go-to options (concrete, beam and block and suspended timber), concrete is the cheapest, and beam and block the most expensive. Basic suspended timber is affordable, but I-joists and open metal web joists are more commonly chosen for their versatility which comes at an added cost.
Average costs (including insulation and labour):
- Suspended timber = £58/m²
- Concrete = £56/m²
- Block and beam = £81/m²
Which floor structures work best with underfloor heating?
Most self builders now fit underfloor heating into their homes. Just how well this works depends, to a great extent, on the floor construction. Concrete floors are ‘high mass’ and will act like a giant storage heater, staying warm for many hours without any heat source.
In contrast, a timber-based floor is relatively ‘low mass’: underfloor heating in a timber floor therefore tends to heat up (and cool down) fairly rapidly, more like a conventional radiator system. So, to benefit from the slow, passive heating of concrete floors, you have to actually be in occupation, preferably 24/7; if you are there for just a few hours a day, you’d be better to opt for a quick-response heating system.
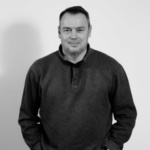
Chartered surveyor Ian Rock FRICS is the author of the Loft Conversion Manual, and is founder of www.rightsurvey.co.uk
Bring your dream home to life with expert advice, how to guides and design inspiration. Sign up for our newsletter and get two free tickets to a Homebuilding & Renovating Show near you.
Chartered surveyor Ian Rock MRICS is a director is Rightsurvey.co.uk and the author of eight popular Haynes House Manuals, including the Home Extension Manual, the Self Build Manual and Period Property Manual.
Ian is also the founder of Zennor Consultants. In addition to providing house surveys, Zennor Consultants provide professional guidance on property refurbishment and maintenance as well as advising on the design and construction of home extensions and loft conversions, including planning and Building Regulations compliance.
Ian has recently added a 100m2 extension to his home; he designed and project managed the build and completed much of the interior fit-out on a DIY basis.