Insulating Floors: What Insulation Do I Need?
When it comes to insulating floors, it can be tricky to know what kind of insulation you need, especially if you are tackling a renovation project
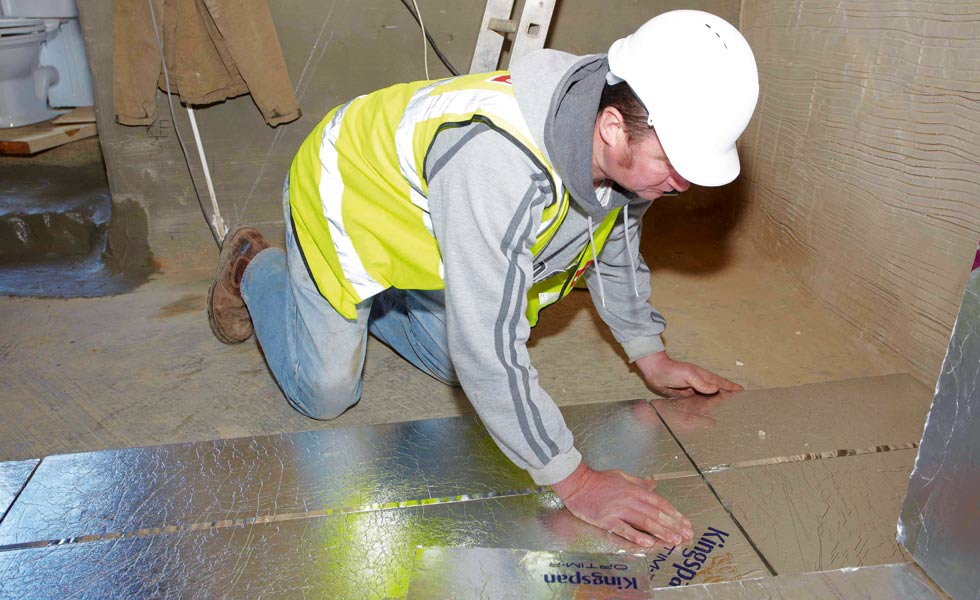
Insulating floors is often trickier than insulating other areas of your home. The ground floor beneath a house is generally warmer than the air around it, and so it would perhaps be third on your list of priorities (behind walls and roofs). However, it makes sense to consider retrofitting, particularly if you have a suspended timber floor.
You can retrofit floor insulation on top of a solid concrete base, too, but this will have an impact on floor height build-up. And it’s only worth digging out the floor if you’re undertaking a major renovation.
(MORE: The complete guide to renovating a house)
The Importance of Insulating Floors
The limiting U value (the maximum U value that cannot be exceeded) required under current Building Regulations are:
- Roof: 0.20W/m²
- Ground floor: 0.25W/m²
- Walls: 0.30W/m²
Heat rises as denser colder air falls and pushes the warmer air up, and is more likely to escape through the roof. And the earth below the ground floor will be warmer (in winter) than the external air, so why does the floor need a better U value than the walls?
To meet the new Target Fabric Energy Efficiency (TFEE) and comply with 2014 Building Regulations, the U values will need to be no worse than 0.13W/m² for both the roof and floor. This recognises that a uniform envelope is a good idea.
(MORE: What is the Green Homes Grant?)
Bring your dream home to life with expert advice, how to guides and design inspiration. Sign up for our newsletter and get two free tickets to a Homebuilding & Renovating Show near you.
Insulating a Solid Floor
Most modern homes have a solid floor, for example:
- concrete slab
- concrete planks
- block and beam
Insulation is laid on the concrete and covered with a screed. There will be a damp-proof membrane under the insulation and possibly a second membrane on top, depending on the type of screed.
In this scenario, a rigid foam insulation is usual, and as you’d want the same U value in the roof, we need the same thickness of insulation (180mm). Many builders will baulk at this figure — it was not long ago that installing 50mm of insulation in the floor was considered fairly advanced.
Insulating a Suspended Timber Floor
A suspended timber floor tends to be cold and draughty because of the air circulating beneath it. Installing any amount of insulation will warm the floorboards and go a long way towards eliminating draughts. The effect is a greater sense of comfort and that, in turn, allows the homeowner to turn the thermostat down.
Typically a renovator does not have to meet the same Building Regulations requirements and has more freedom in the amount of insulation installed. On the other hand, the noticeable impact of the insulation is likely to be greater.
Achieving a U value of 0.25 would be a good target. That would need 90mm of rigid foam or 150mm mineral wool. A semi-rigid material is generally best as it can be cut very slightly oversized and squeezed in between the floor joists, thereby ensuring no draught-causing gaps.
The insulation should be pushed tight to the underside of the floorboards. At least 25mm of the joist must be left exposed to ensure air circulation. This is to prevent the joist becoming damp and encouraging dry rot. For the same reason, any airbricks must be left clear to ensure a good air flow.
The way the insulation is installed will vary with the type and rigidity of the insulation:
- Rigid foams just need a few tacks to ensure they do not drop
- Semi-rigid batts will need battens fixed along the joists
- Flexible wools will need battens across the joists.
The thickness required to achieve a U value of 0.25W/m² on a suspended floor is:
- Mineral wool: 150mm
- Rigid foam: 90mm
Space Blanket
This is fibreglass insulation encapsulated in a metalised polythene film. It is said to be more effective than simple fibreglass, as the metalised film reflects heat. It is useful in hard-to-reach spaces and under suspended floors as it can be tacked into place.
Retrofit Floor Insulation
Installing insulation on top of the floor can present problems with ceiling, door and window cill heights. Kingspan’s new range of Vacuum Insulated Panels (VIPs) offers an interesting solution for those needing an ultra-thin build-up.
The panels consist of a microporous core, which is evacuated and sealed in a thin, gas-tight membrane. They can achieve performance similar to the thickness of traditional insulation at levels of just 26mm.
Tim is an expert in sustainable building methods and energy efficiency in residential homes and writes on the subject for magazines and national newspapers. He is the author of The Sustainable Building Bible, Simply Sustainable Homes and Anaerobic Digestion - Making Biogas - Making Energy: The Earthscan Expert Guide.
His interest in renewable energy and sustainability was first inspired by visits to the Royal Festival Hall heat pump and the Edmonton heat-from-waste projects. In 1979
this initial burst of enthusiasm lead to him trying (and failing) to build a biogas digester to convert pig manure into fuel, at a Kent oast-house, his first conversion project.
Moving in 2002 to a small-holding in South Wales, providing as it did access to a wider range of natural resources, fanned his enthusiasm for sustainability. He went on to install renewable technology at the property, including biomass boiler and wind turbine.
He formally ran energy efficiency consultancy WeatherWorks and was a speaker and expert at the Homebuilding & Renovating Shows across the country.