Building material prices and availability see positive trends, so could now be a good time to build your new home?
We break down the key figures for building materials prices and why now could be a good time to build your new home
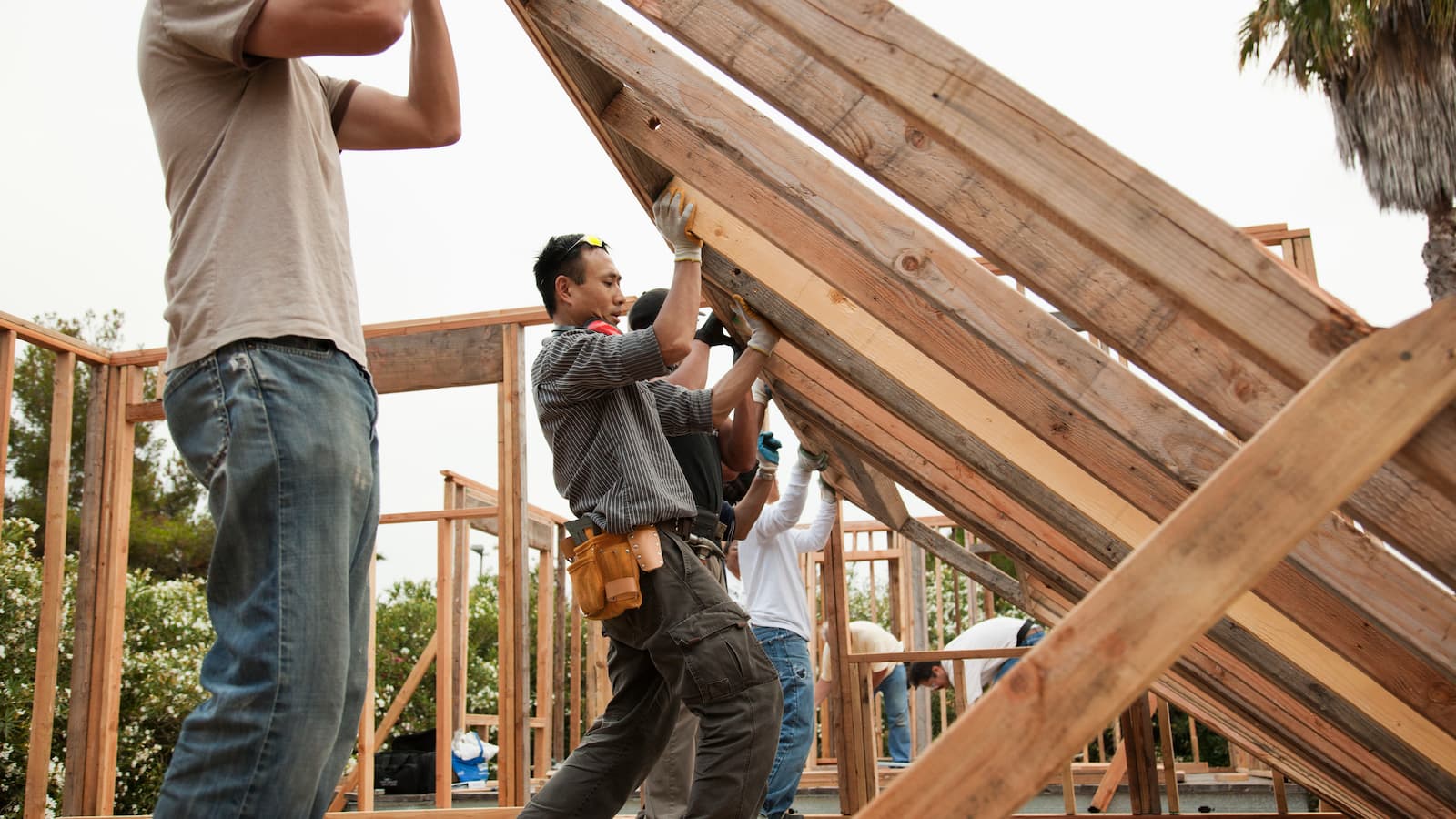
Building materials prices and rising availability could make building new homes a lot easier, according to the latest government statistics.
After a turbulent period marked by significant price fluctuations and supply chain disruptions, the construction industry is starting to stabilise. In particular, building material prices, including those for essential components like bricks and concrete blocks, have shown positive trends.
We dive into the current state of the market, including key material prices, and how this will influence how much it costs to build a house.
Rising availability for key building materials
For anyone planning to build a new home, the recent uptick in building material availability is a welcome sign, according to the government's latest building materials prices index.
Deliveries of essential materials like bricks and concrete blocks are on the rise. Specifically, deliveries of bricks have increased by 8.5% compared to January 2024, while concrete blocks saw a 4.2% increase. This is a significant improvement from the shortages and delays that hampered the industry during the peak of the COVID-19 pandemic and its aftermath.
Alongside these increases in supply, building material prices are stabilising, making it a potentially good time to invest in construction. The materials essential to building your dream home are becoming more readily available, with fewer concerns over scarcity. However, prices, while somewhat lower than their peak in 2022, are still higher than the historical norms, though they have levelled out considerably over the last few months.
For example, the cost of construction materials like precast concrete and blocks has seen moderate rises, but these are far less severe than the sharp increases experienced between 2020 and 2022.
Bring your dream home to life with expert advice, how to guides and design inspiration. Sign up for our newsletter and get two free tickets to a Homebuilding & Renovating Show near you.
Construction materials experiencing the greatest price increases and decreases in the 12 months to March 2025, according to the government's latest Building Materials and Components Statistics
Greatest price increases
- Other builders’ ironmongery +9.5%
- Precast concrete: blocks, bricks, tiles and flagstones +6.8%
- Pre-cast concrete products +5.1%
Greatest price decreases
- Fabricated structural steel -10.0%
- Concrete reinforcing bars (steel) -5.1%
- Pipes and fittings (rigid) -4.6%
Building materials market stability following post-2022 volatility
The construction market has undergone significant volatility, especially between 2020 and 2022, when the industry experienced sharp price hikes due to supply chain disruptions, material shortages, and increased demand.
Prices for essential materials like cement, bricks, and concrete skyrocketed, making it difficult for builders to predict costs and timelines.
Now, with the market stabilizing, 2025 offers a more predictable environment for those looking to build a new home. Although material prices remain elevated compared to pre-pandemic levels, the volatility seen in 2020-2022 has largely subsided. This gives builders and homeowners more confidence that material prices will not unexpectedly spike during construction.
In fact, the material price index for "All work" decreased by 0.9% in January 2025 compared to the same time last year, signalling that material costs may be easing, even if they remain higher than usual.
What does the current construction market look like?
Looking at the broader construction market, 2025 shows encouraging signs, particularly for private housing.
According to the Bank of England’s most recent update, the rate of decline in construction output is easing, and there’s optimism that modest growth will return in the first half of 2025. Private housebuilding, which accounts for much of the demand for building materials, has rebounded, with output recovering to levels seen a year ago.
While this is promising, there are still concerns that could impact your decision to start building now. Social housing projects, which tend to rely on public funding, are facing constraints due to financial pressures and difficulties in securing land.
This has, in turn, placed additional strain on the availability of materials for private projects as social housing providers also compete for resources. Builders should keep this in mind when estimating timelines and availability.
Supply chain and labour challenges
Though building material prices and availability are improving, challenges remain. Supply constraints such as planning delays and labour shortages are still limiting construction growth.
The Construction Leadership Council (CLC), Federation of Master Builders (FMB), and Building Employers Confederation (BEC) have all expressed concerns that, while the demand for new builds remains strong, the supply side of the equation – such as the availability of skilled labour and contractors – could delay projects.
Tight labour markets have been an ongoing issue, compounded by a backlog in planning applications that might add to the timeline for getting your project off the ground.
Additionally, even though material prices have stabilised, other aspects of the construction process, such as labour costs and planning approval delays, could still affect the overall cost and timeline of your new home.
Builders are finding it challenging to secure enough skilled workers, which could result in longer waits for construction to begin and potentially higher labour costs.
Falling inflation boosts building materials prices
Need more advice or inspiration for your project? Get two free tickets to the Homebuilding & Renovating Show.
UK inflation, which unexpectedly dipped to 2.5% in December 2024, has further contributed to optimism in the industry.
A potential interest rate cut in the near term may help stabilise costs, creating favourable conditions for manufacturers and builders as they tackle ambitious housing and infrastructure projects.
As 2025 unfolds, the construction sector's resilience and adaptability will be tested, but the rise in building material purchases and the alignment of public investment with private sector demand offer a promising outlook for the industry.
Is now the right time to build?
Given the current trends in building material prices and the broader construction market, now could be a good time to build your new home.
Key materials like bricks and concrete blocks are more available, and prices have stabilised, making it easier to plan your budget. The easing of construction output decline and the recovery of private housebuilding are positive indicators for those looking to break ground in 2025.
Ultimately, whether it’s the right time to build will depend on your specific circumstances. If you’re ready to move forward with your dream home and can plan for the potential challenges, the trends indicate that conditions are more favourable than they have been in recent years.
With building material prices seeing positive trends and rising availability, 2025 may be an ideal time to get started building your new house.
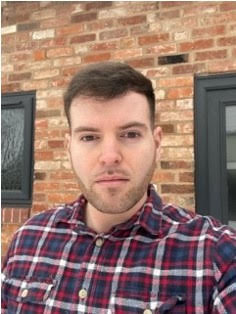
News Editor Joseph has previously written for Today’s Media and Chambers & Partners, focusing on news for conveyancers and industry professionals. Joseph has just started his own self build project, building his own home on his family’s farm with planning permission for a timber frame, three-bedroom house in a one-acre field. The foundation work has already begun and he hopes to have the home built in the next year. Prior to this he renovated his family's home as well as doing several DIY projects, including installing a shower, building sheds, and livestock fences and shelters for the farm’s animals. Outside of homebuilding, Joseph loves rugby and has written for Rugby World, the world’s largest rugby magazine.